Bipolar plates are crucial components in everything from proton exchange membrane (PEM) fuel cells and alkaline fuel cells to solid oxide fuel cells and electrolyzers. Each plate serves a dual role: they distribute gasses and air through carefully machined flow fields or channels while also conducting electrical current between stacked cells. Given the intricate requirements for gas and fluid flow, electrical conductivity, and structural integrity, bipolar plates are fundamental to the performance of these electrochemical devices.
The challenge for manufacturers is in producing precise bipolar plates that are both highly durable and highly corrosion resistant – especially when using complex materials like titanium. With plates required to perform without failure in the high pressures and temperatures of electrochemical reactions, you need a process that can deliver intricate designs with exceptional precision and minimal material waste.
As the world’s largest titanium photochemical etching manufacturer, PEI leads the way in fabricating high-performance metal components. Our industry-leading precision chemical machining technology offers a precise, durable, and reliable solution for manufacturing bipolar plates. We combine digital tooling and cost-effective methods to quickly adapt designs, minimizing lead times and maximizing efficiency for clients across various industries.
In this article, we explore why precision chemical machining is the proven process for bipolar plates, its advantages over traditional machining methods, and common applications of PCE-manufactured bipolar plates.
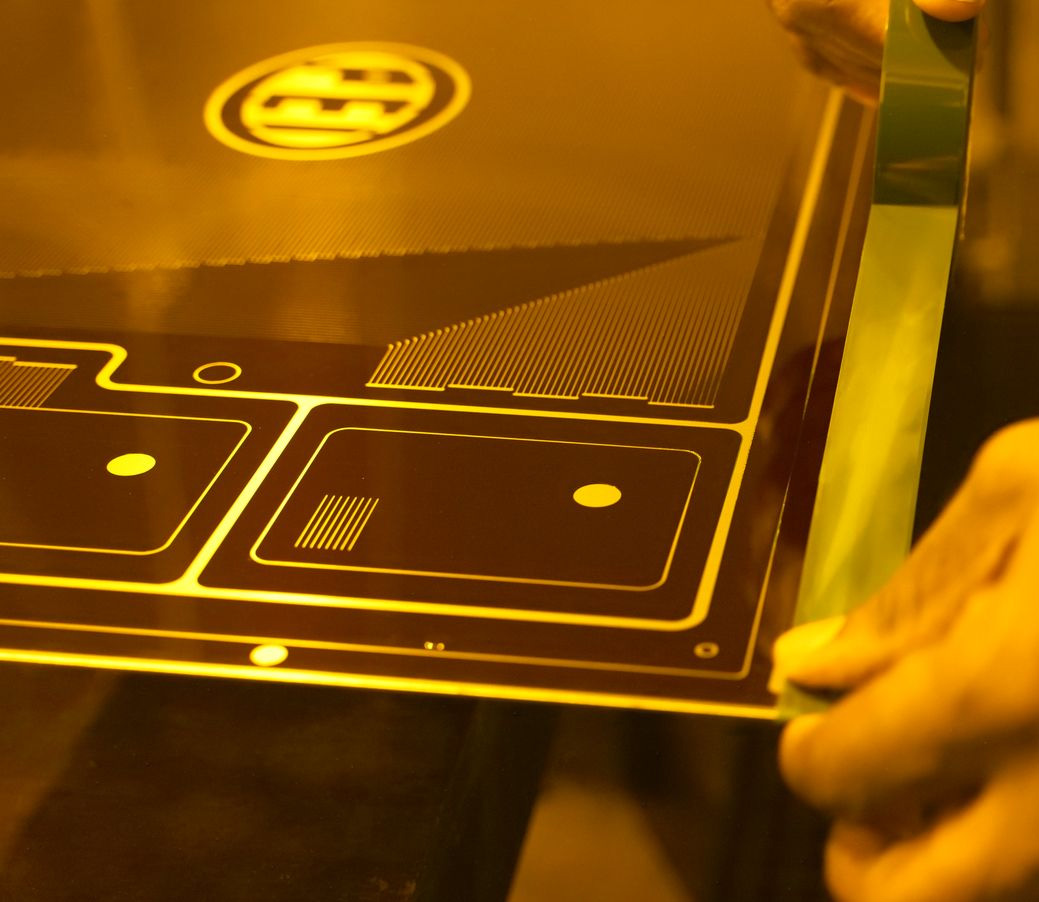
Why Precision Chemical Machining Is Ideal for Bipolar Plate Manufacturing
With its ability to produce intricate designs with exceptional precision and minimal material waste, precision chemical machining, aka photochemical etching, has become the trusted process for many manufacturers. The process involves the simultaneous removal of metal, allowing for the creation of complex flow fields on both sides of the plate. Unlike traditional methods such as stamping or hydroforming, precision chemical machining introduces no mechanical stress, burrs, or deformations that could compromise the plate’s performance.
Precision and Complexity
Precision chemical machining enables the creation of highly detailed and complex flow field channels, which are essential for the efficient operation of fuel cells and electrolyzers. The accuracy of the etched designs ensures that gasses and liquids flow smoothly through the channels, improving the device’s overall efficiency.
Unlike other machining methods, this innovative process doesn’t stress the material, making it ideal for producing sheet metal parts like bipolar plates, where maintaining material integrity is critical.
Material Versatility
Titanium is one of the most challenging materials to work with, but its unique properties—corrosion resistance and high conductivity—make it a top choice for bipolar plates. Precision chemical machining works perfectly with titanium and a range of other materials, allowing manufacturers to achieve the exacting tolerances required without compromising the material’s natural properties. The versatility of this process makes it suitable for a wide range of metals commonly used in fuel cells and other energy applications.
Scalability
The scalability of precision chemical machining makes it ideal for both prototyping and mass production. Whether producing small quantities for testing or large volumes for commercial use, the process remains cost-effective while delivering the same high level of precision across all units. This is crucial for industries like automotive and aerospace, where consistent performance is a non-negotiable requirement.
No Heat-Affected Zones or Mechanical Stress
One of the most significant advantages of precision chemical machining is that it avoids the heat-affected zones and mechanical stress common in other processes, such as stamping or laser cutting. These traditional methods can introduce unwanted stresses, distortions, or thermal deformations, which may compromise the bonding of the stack or reduce the plate’s overall efficiency. Precision chemical machining eliminates these issues, ensuring that the bipolar plates maintain their structural integrity and deliver optimal performance.
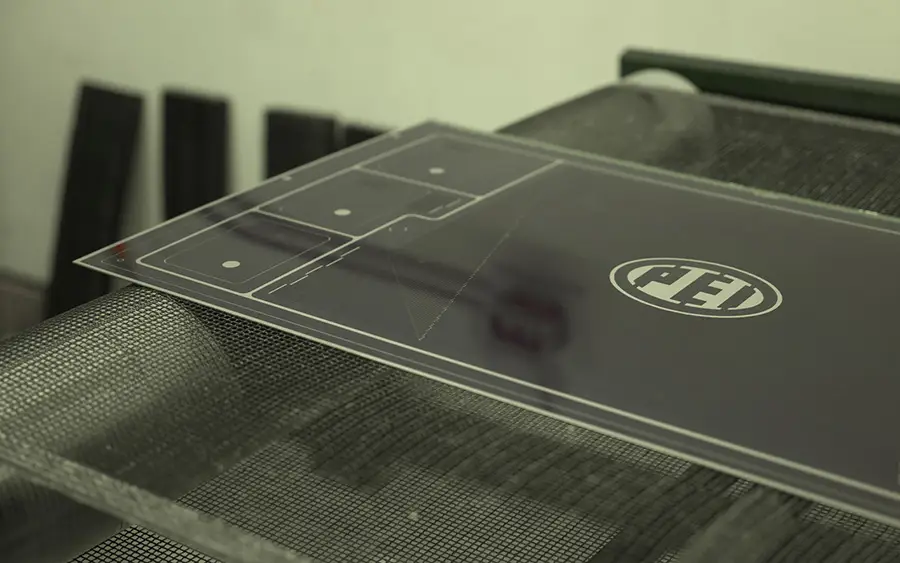
Advantages Over Other Manufacturing Processes
While stamping, hydroforming, and laser cutting are common alternatives for manufacturing metal components like bipolar plates, they each have limitations.
Plates typically require precise flatness to ensure optimal performance, but stamping and hydroforming can affect their planarity and introduce mechanical stresses or burrs that may impede functionality, especially in applications requiring two bipolar plates to stack effectively. These traditional methods can also compromise the plate’s ability to provide electrical conduction and handle liquid coolant flow efficiently, which are critical for maintaining the usable output voltage in a membrane electrode assembly.
The tooling costs for these methods can also be prohibitive, particularly for prototyping, as they require the creation of expensive, time-consuming dies.
Compared to Stamping and Laser Cutting
In contrast to stamping and laser cutting, precision chemical machining offers superior flexibility and precision without compromising the material’s properties. Laser cutting often introduces heat, which can cause thermal deformations, while stamping can induce mechanical stress that affects the bonding of the plates in fuel cell stacks. Precision chemical machining avoids both issues, ensuring the final product is defect-free and ready for high-performance applications.
Material Efficiency
Precision chemical machining also minimizes material waste, making it an environmentally friendly manufacturing process. By selectively removing material without the need for expensive tooling or extensive setup, manufacturers can reduce production costs while achieving high levels of precision. PEI’s precision chemical machining is particularly well-suited for titanium, a preferred material for bipolar plates due to its corrosion resistance and excellent conductivity. This process also works seamlessly with other metals, ensuring that manufacturers can meet the stringent requirements of polymer electrolyte membrane (PEM) fuel cells and electrolyzers without compromising material properties.
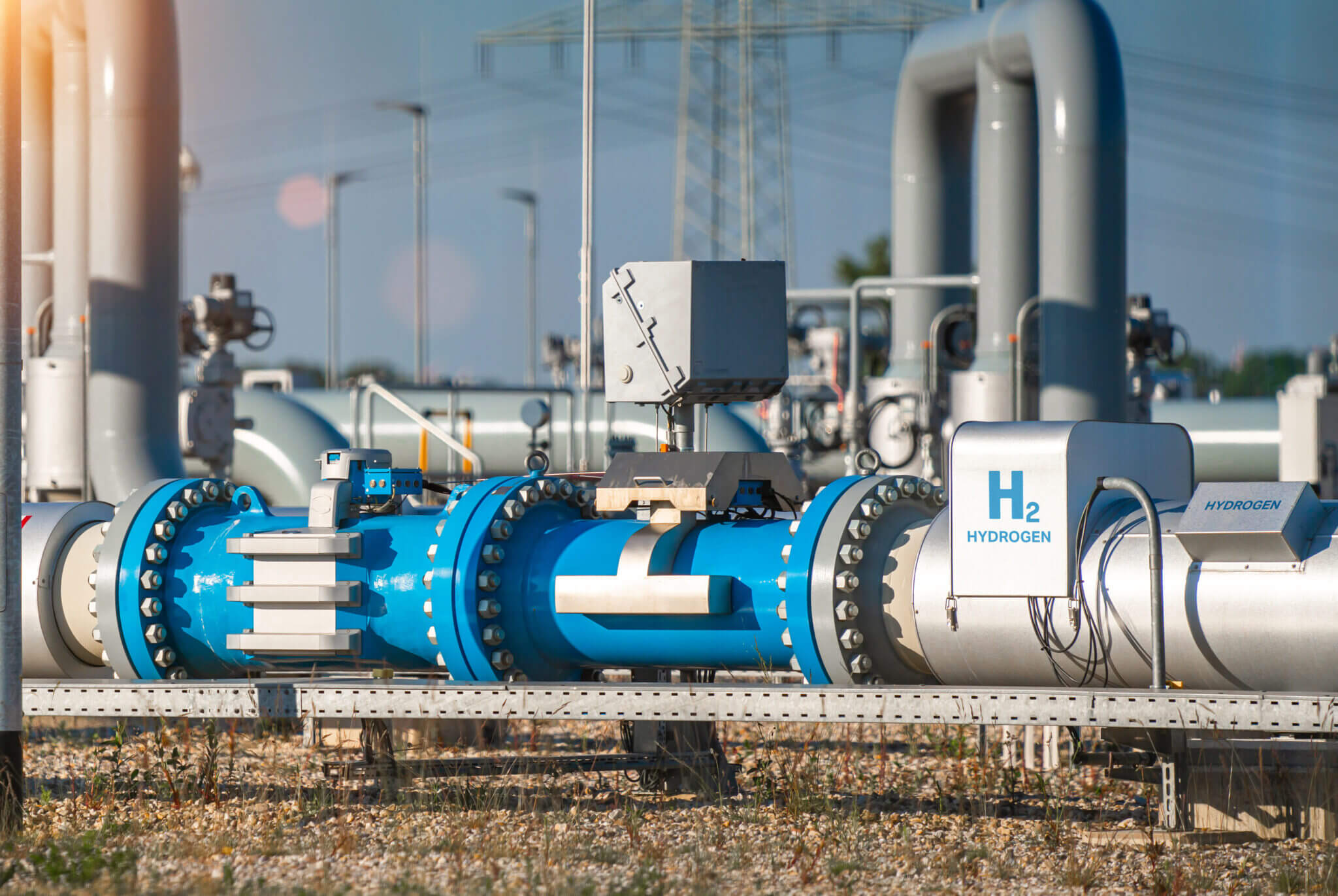
Applications of Bipolar Plates Manufactured via Precision Chemical Machining
Precision chemical machined bipolar plates are key components for a wide variety of critical electrochemical applications in typical operating conditions.
In the automotive industry, bipolar plates power fuel cells, providing a high-performance power solution for on- and off-road vehicles. With proven reliability and industry-leading efficiency, Nuvera E-Series Fuel Cell Engines provide a high-performance power solution for on- and off-road vehicles, maritime vessels, and stationary and portable generators. Today, Nuvera fuel cell engines power buses, trucks, container handling equipment, and many more medium- and heavy-duty applications.
High-performance bipolar plates are also key components in components in hydrogen production for fuel cells. The FCgen®-HPS, for example, is a high-power density, carbon fibers-reinforced, hydrogen fuel cell. The FCgen®-HPS for example, is a high-performance, high-power density, liquid-cooled fuel cell stack designed to provide propulsion for a range of light-, medium- and heavy-duty vehicles.
The aerospace sector also relies on bipolar plates for lightweight, high-performance energy systems, while these powerful plates are also critical in energy storage and power generation devices, where durability and precision are key to maintaining long-term performance.
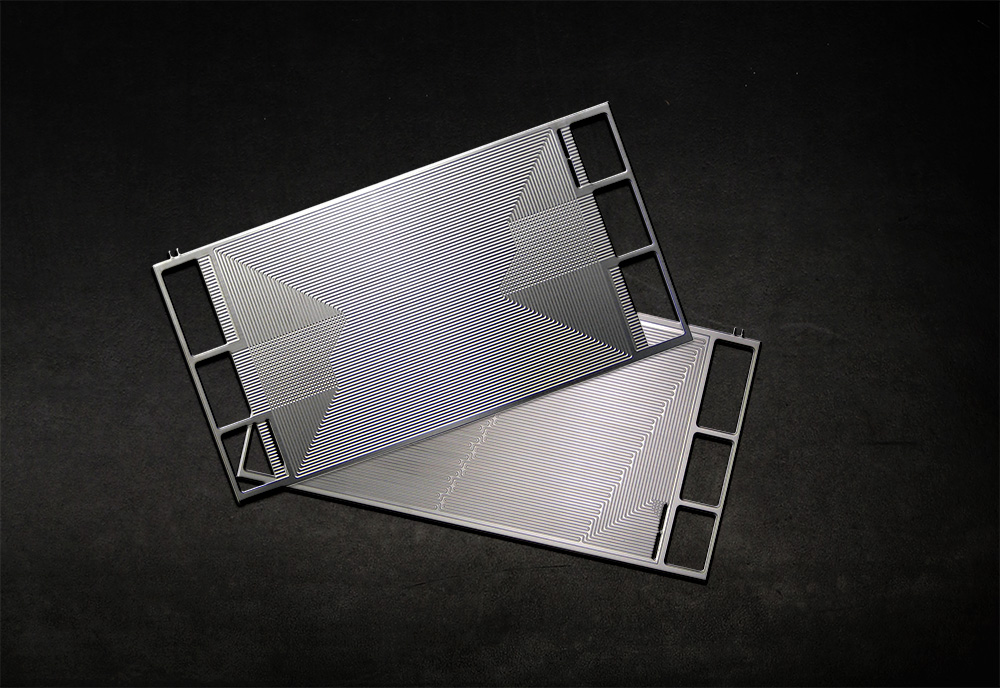
Ensuring Precision and Performance in Bipolar Plate Production
When it comes to producing high-precision bipolar plates, especially for applications that require complex flow fields and high-performance materials like titanium, one process stands out above the rest. With its ability to deliver intricate, stress-free designs with minimal material waste and scalability, precision chemical machining is far superior to traditional manufacturing processes like stamping and laser cutting.
As the world leader in precision chemical machining, PEI has become a trusted manufacturing partner for delivering precise, durable, and reliable quality parts you won’t find anywhere else. With decades of experience and a daily dedication to perfection, we consistently produce stress-free metal parts with efficiency, accuracy, and cost-effectiveness.