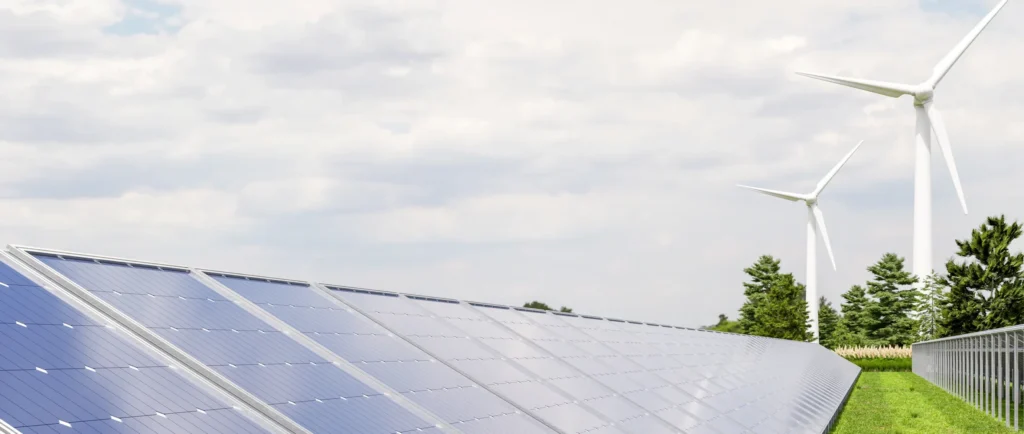
Discover how the photochemical etching of titanium is revolutionizing high-performance energy applications. Titanium’s exceptional properties, including corrosion resistance, lightweight nature, and strength, make it ideal for energy-related technologies.
Titanium is one of the most dependable materials available for manufacturers producing metal parts via photochemical etching thanks to its strength, corrosion resistance, and compatibility characteristics.
While producing parts used in various applications within the energy industry, chemical etching titanium produces strong, lightweight parts that are resistant to both corrosion and high temperature. Titanium’s smooth surface also limits the adhesion of foreign materials, reducing contamination from outside sources.
As an industry leader in titanium etching, the Photofabrication Engineering, Inc. (PEI) team has a long history of engineering and manufacturing excellence. We were one of the first manufacturers to chemically machine titanium and have quickly become the global production leader.
Over the years, we’ve developed expertise in this complex process and meet the most stringent international certification standards. Today, PEI is a leader in producing photochemically-etched titanium electrolyzer bipolar plates and other critical parts and components for high-performance energy applications.
In this article, we explore the crucial role chemical machining of titanium plays in high-performance energy applications and the many benefits it delivers.
The crucial role of high-performance energy applications
Today’s energy market is in a rapid state of transition as it moves towards a more sustainable future. Every acceleration towards that shift for more efficient and sustainable energy solutions increases the demand for high-performance energy applications.
High-performance energy applications deliver superior performance compared to conventional energy systems, enabling optimized energy generation, transmission, and consumption.
Titanium, and photochemically machining of titanium, play a crucial role in delivering such applications. The metal and its alloys feature exceptional properties, including a high strength-to-weight ratio, excellent corrosion resistance, and biocompatibility, making it a sought-after material for energy-related technologies.
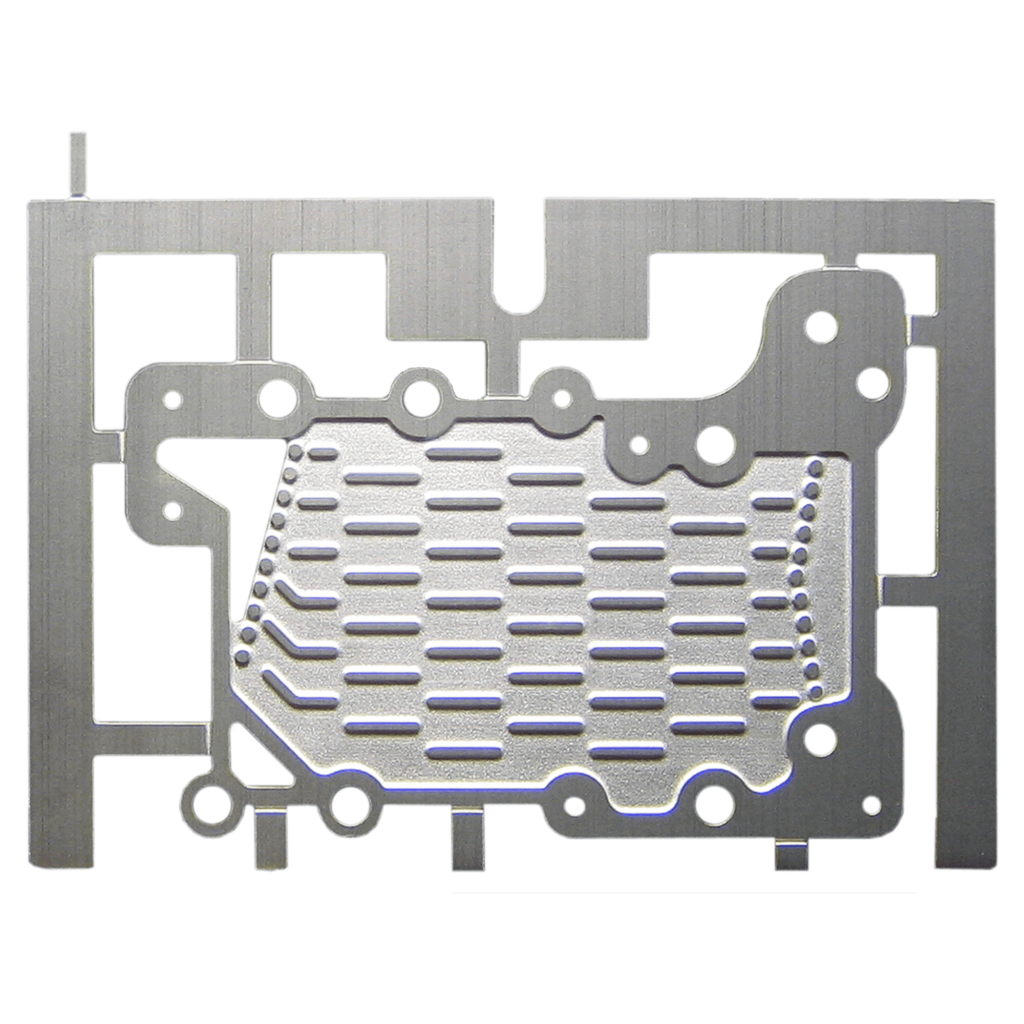
Companies use titanium parts and components in advanced solar panels, electrolyzer bipolar plates, fuel cells, batteries, and high-efficiency turbines. These chemically etched titanium components increase energy conversion efficiency, promote sustainability, and contribute to the global transition towards cleaner and more efficient energy sources.
The team at PEI are experts in titanium etching for the energy sector, producing anodes and cathodes for the fuel cell industry, parts and components for solar and renewable energy generation applications (including fuel cells, batteries, nuclear power applications and desalination systems). Our unique capabilities and specialized titanium etching processes enable us to etch to multiple depths within the same part all burr free and stress free.
High-performance energy applications in action
High-performance energy applications are vital in the transition to clean and renewable energy sources. Embracing and deploying these applications is critical for achieving a sustainable, resilient, low-carbon energy future.
Titanium is at the center of many of these applications, especially in the form of photochemically-etched Bipolar Electrolyzer plates.
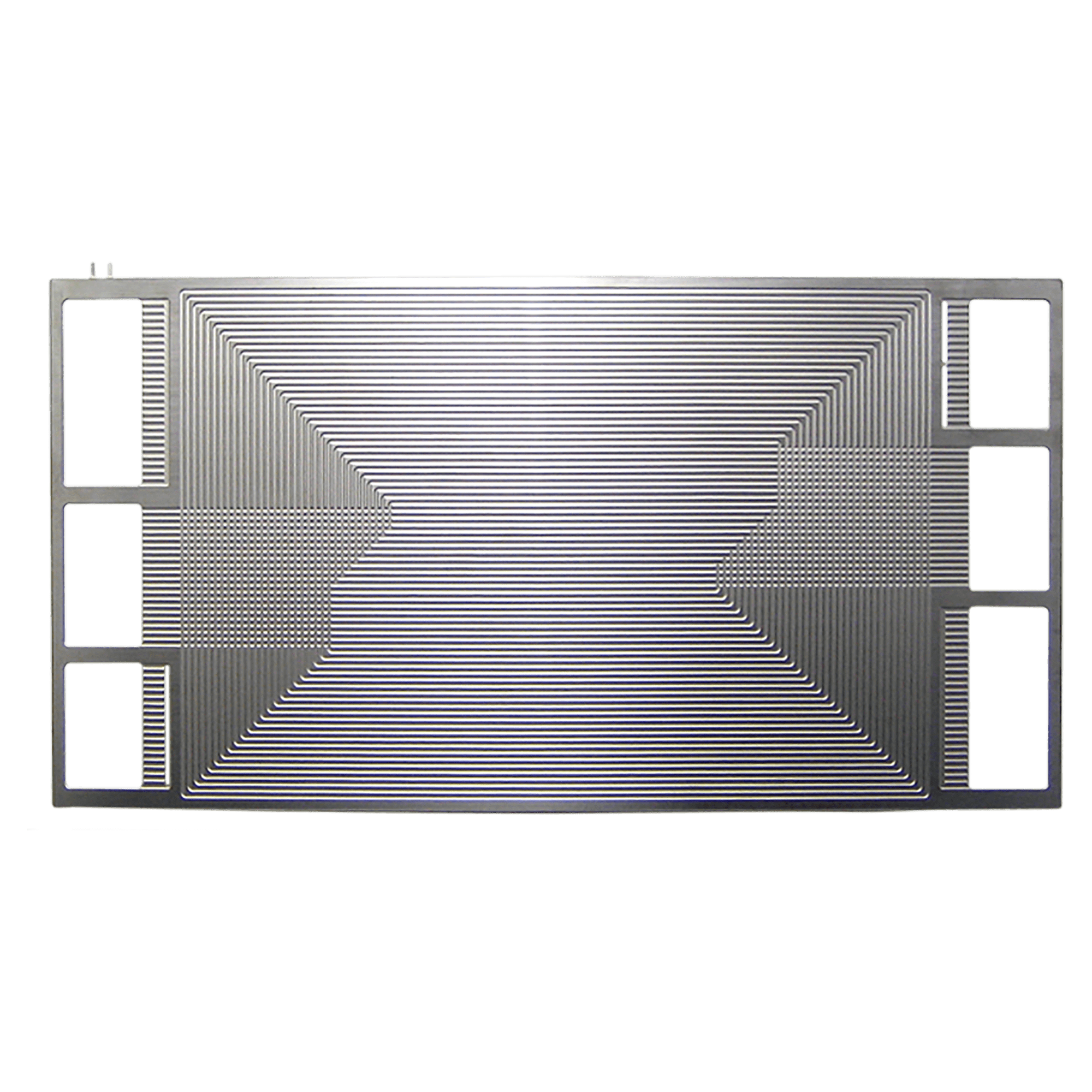
You’ll find Bipolar Electrolyzer plates in these applications:
Hydrogen Production
Water electrolysis systems use bipolar electrolyzer plates to produce hydrogen gas. The plates serve as electrodes through electrolysis, allowing water to be split into hydrogen and oxygen. With bipolar plates, hydrogen can be produced efficiently with improved energy conversion and high current density.
Energy Storage
Titanium bipolar electrolyzer plates are at the heart of hydrogen generators which can easily convert excess renewable energy into a more easily stored energy source…Hydrogen. They convert renewable energy, like solar or wind power, into hydrogen or other energy sources that can be stored for later use during high energy demand or limited renewable energy supply — balancing out the unpredictable nature of renewable energy sources.
Fuel Cells
Bipolar Electrolyzer plates are used in fuel cell systems as electrodes to convert hydrogen or other fuel sources into electrical energy. They ensure efficient electrical current distribution and play a crucial role in maintaining the fuel cell stack’s performance and durability.
Titanium is also used for various solar and energy generation applications, including fuel cells, batteries, and nuclear and desalination systems, which is why titanium etching is such an in-demand process.
Titanium fuel cells, oxygen generators, and hydrogen generators represent a giant step in developing renewable energy technology. With every component reliant on precisely etched titanium parts, titanium etching experts like PEI are playing an increasingly important role within the energy sector.
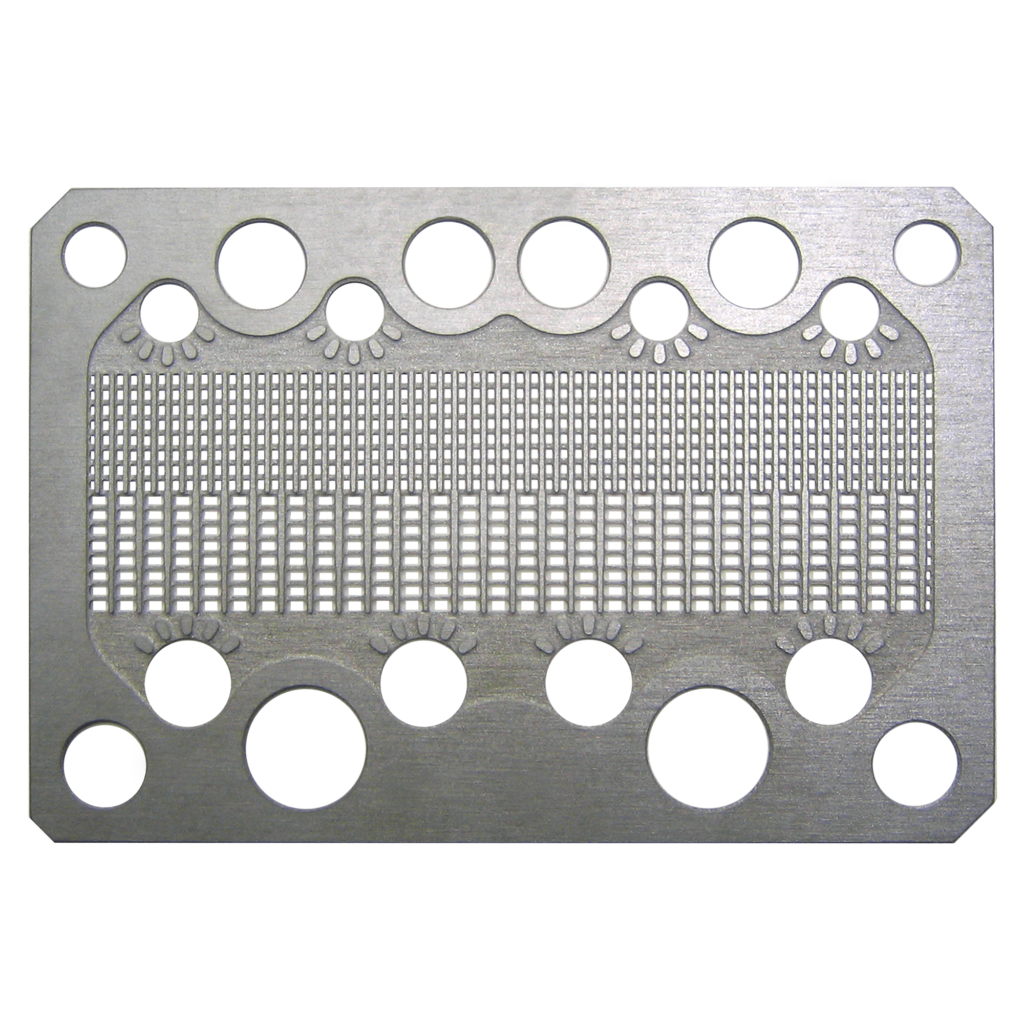
The critical role of Titanium and titanium etching in energy applications
Due to its versatility and high performance, titanium’s unique properties make it ideal for various energy-related technologies. Its exceptional strength-to-weight ratio, resistance, and high-temperature stability make it invaluable in demanding environments, making it the perfect metal for many critical energy applications.
Corrosion Resistance
Non-corrosive metals like titanium are ideal for use in challenging environments in energy generation processes. It can withstand exposure to aggressive substances, such as high-temperature fluids, chemicals, and saltwater, without significant degradation. This corrosion resistance ensures the longevity and reliability of equipment and structures in energy generation systems.
High Strength-to-Weight Ratio
Titanium’s lightweight and high strength-to-weight ratio is ideal for energy generation applications where weight reduction is desirable, such as in marine-based renewable energy systems. Using lightweight yet strong materials allows for more efficient energy conversion, transportation, and installation processes.
Heat Resistance
Titanium can withstand high temperatures without deformation or degradation, making it perfect for applications involving extreme heat, such as gas turbines, heat exchangers, and nuclear power systems. Maintaining structural integrity at elevated temperatures ensures reliable and efficient energy generation processes.
The titanium etching process
Regarding the best process to etch titanium, photochemical etching is preferred due to its ability to produce accurate and repeatable shapes consistently. Photochemical etching, also known as chemical milling or photo etching, is a precise and versatile process used to fabricate intricate patterns and structures on titanium parts.
The titanium etching process involves several key steps.
One — titanium sheets are first cleaned and coated with a light-sensitive photoresist material
Two — a photomask is placed on the coated sheets containing the desired pattern.
Three — ultraviolet light is passed through the photomask, exposing the photoresist in the desired areas. After exposure, the unexposed photoresist is removed, leaving only a protective layer in the patterned regions.
Four — the titanium sheets are then immersed in an etchant solution (hydrofluoric acid/ nitric acid) that selectively dissolves the exposed areas, resulting in the desired pattern etched into the metal surface.
Five — The etched part is thoroughly rinsed, and the remaining photoresist is stripped away, leaving behind the final etched titanium part with precise dimensions and intricate features.
This photoetching process offers excellent precision, repeatability, and scalability for etched titanium parts, making it an efficient and cost-effective method for producing high-quality titanium parts with complex geometries.
Some of the key benefits of this titanium etching process include
Complex Geometries:
The process enables the creation of intricate designs, thin walls, and fine details, ideal for applications requiring lightweight and precise titanium components. This applies to various titanium grades.
Cost-Effectiveness:
Photochemical etching of titanium also eliminates the need for expensive tooling and complex setups, reducing production costs, especially for small to medium-sized runs.Material Preservation: The process retains titanium’s strength, corrosion resistance, and other properties since it does not generate heat or induce mechanical stress.
Scalability and Versatility:
Photochemical etching can be applied to different shapes and sizes of titanium components, accommodating various production volumes and grades of titanium alloys.
Titanium etching and the future of the solar and energy generation market
As the energy sector transitions to more sustainable energy options, the reliance on titanium and the titanium etching process will continue to grow.
Experts in chemical etching titanium, PEI will continue to produce photochemically-etched Bipolar Electrolyzer plates for the solar and energy generation markets. Titanium fuel cells, oxygen generators, and oxygen and hydrogen generators, all made by PEI, also represent a giant step in developing clean energy technology.
For an energy partner you can rely on, contact the team at PEI or request a quote.
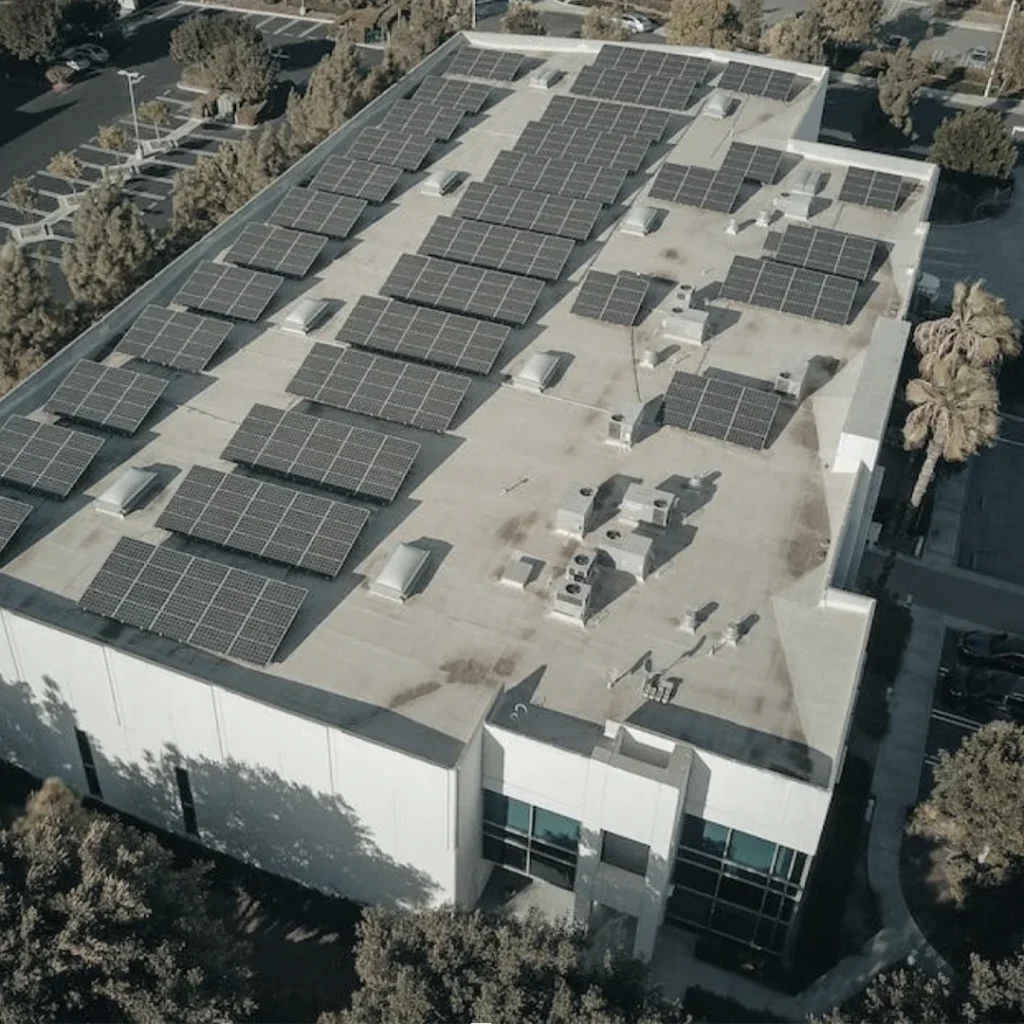