Delicate components are critical to renewable energy industries, maximizing energy conversion and ensuring the longevity and sustainability of renewable energy infrastructure.
But for these delicate components to withstand the harsh environments renewable technologies face, you need a metal with the properties to perform. With its unique combination of strength, low weight, excellent corrosion resistance, and biocompatibility, titanium has become the trusted material for delicately etched components that are relied on across the industry.
PEI is a renowned photochemical etching company specializing in precision components, particularly in the renewable energy sector. With a focus on innovation and quality, PEI has established itself as a trusted partner for clients seeking intricate and reliable titanium components for various renewable energy applications.
In this article, we look at the advantages of titanium in renewable energy technologies, its key applications, and how these parts and processes shape the future of the renewable energy industry.
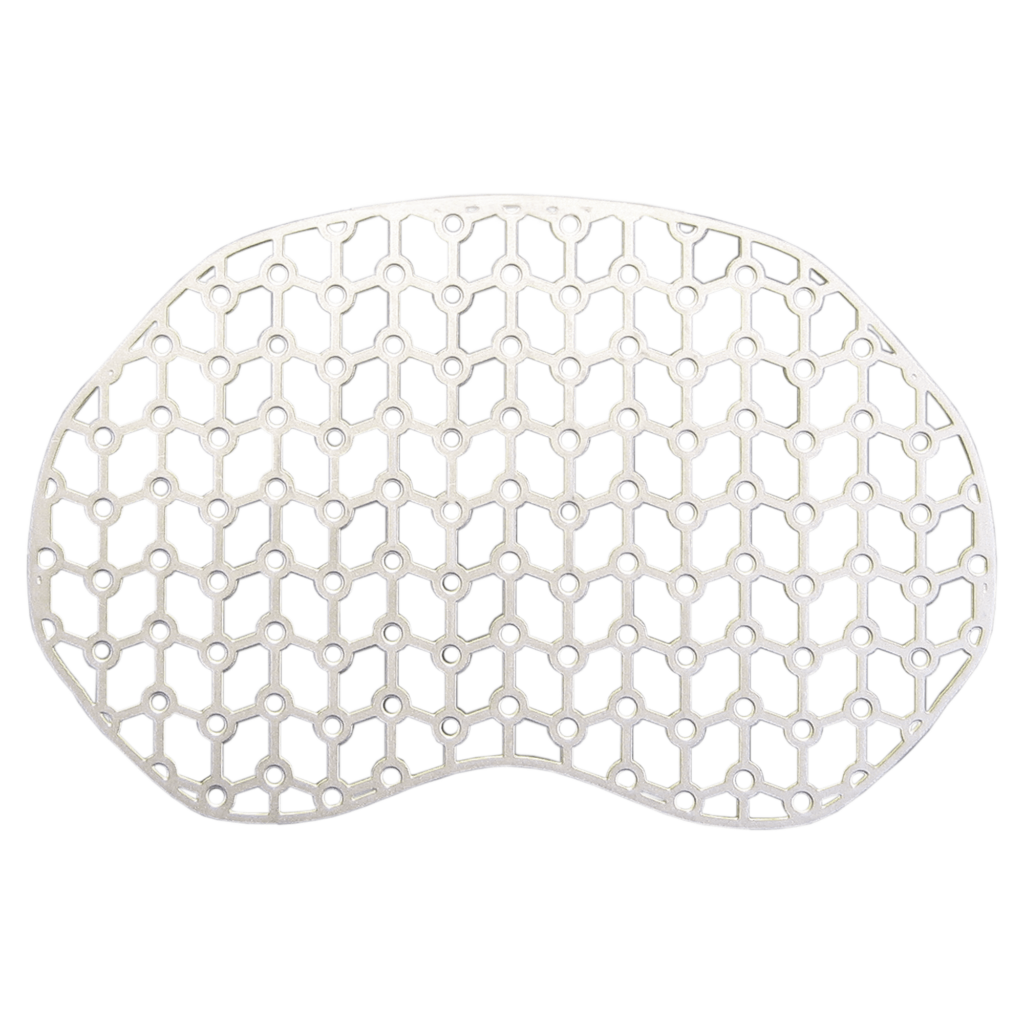
Understanding Titanium Etching
Photochemical etching, also known as chemical milling or chemical etching, is a highly precise manufacturing process that selectively removes material from metal sheets by applying an etching solution and UV light.
Due to its precision and versatility, the photochemical etching process is the ideal choice for producing delicate, titanium-etched parts.
This process involves masking the titanium sheet with a light-sensitive photoresist material and exposing it to UV light through a photomask, which defines the desired pattern on the metal surface. The exposed areas of the photoresist harden, while the unexposed areas remain soluble.
The unexposed photoresist is removed by developing the sheet and exposing the underlying titanium. This titanium is then etched off using chemical solutions, such as hydrofluoric acid, to reveal the intricate pattern on the titanium sheets.
Compared to traditional machining methods, titanium etching offers a range of advantages, including a high strength-to-weight ratio, corrosion resistance, and biocompatibility.
As one of the first manufacturers to etch pure titanium, PEI’s expertise in this complex process is leveraged across multiple industries. Our advanced titanium etching process delivers lightweight, robust, and corrosion-resistant titanium parts, from medical implants like pacemakers to aerospace components and hydrogen electrolyser plates. The smooth surface finish of our etched titanium components minimizes material adhesion, thereby reducing contamination risks.
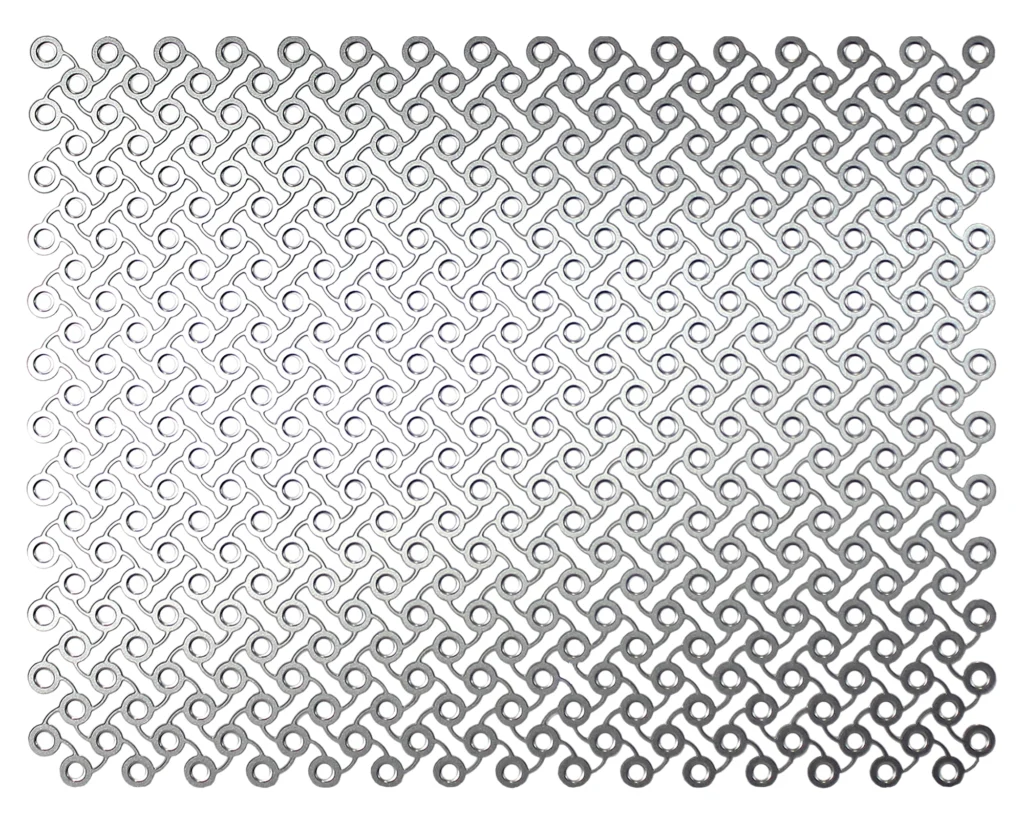
The Key Applications of Photochemically Etched Titanium
In aerospace applications, photochemically etched titanium components are utilized in aircraft structures, engine components, and fuel system parts, where lightweight yet robust materials are paramount. In the medical field, titanium etching enables the production of surgical instruments, implants, and prosthetics with precise geometries tailored to patient-specific needs.
Titanium etching also plays a big part in the electronics industry. Due to its conductivity and durability, especially with titanium alloys, it’s used to manufacture intricate electrical components, connectors, and shielding materials.
In the renewable energy sector, titanium etching facilitates the production of components for high-performance vehicles and renewable energy systems, such as heat exchangers, turbine blades, and fuel cells.
PEI produces a wide range of photo-etched titanium parts for the renewable energy/power industry. They include:
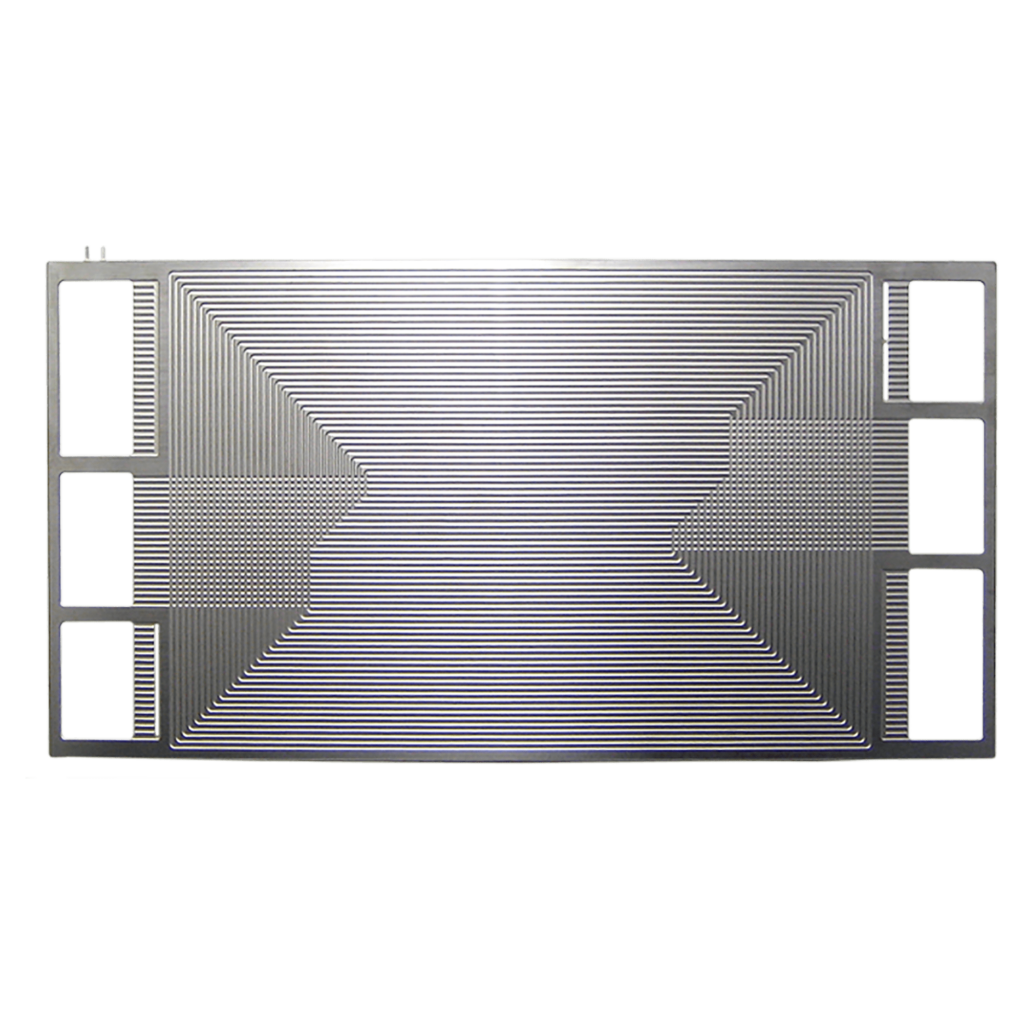
Bipolar Electrolyser Plates
PEI has become a leader in the renewable energy sector, providing pure titanium bipolar electrolyser plates for the solar and energy generation markets. Our photochemical machining process allows very large, very thin single- or double-sided plates to be etched without incurring the stresses typical of other machining methods. Dimensions can be held to extremely high tolerances, and the process yields exceptionally smooth surfaces and channels (even with multiple channel depths on the same plate), free of burrs and other surface irregularities.
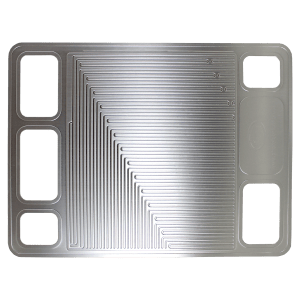
Anodes and Cathodes
Photofabrication Engineering (PEI) etches pure titanium to create anodes and cathodes for the fuel cell industry. As the leading expert in etching exotic materials and titanium for a broad variety of solar and energy generation applications (including fuel cells, batteries, and nuclear and desalination systems), PEI’s unique capabilities allow us to etch metals to multiple depths without the resist failures common to this etching process.
Chemical Etching Titanium: The Advantages for Renewable Energy
Titanium’s exceptional flexibility has enabled the creation of intricate, durable components for a variety of key applications right across the renewable energy sector.
This innovative photochemical etching process offers a range of benefits to both manufacturers and end users, making it the ideal choice for applications where precision, performance, and durability are non-negotiable. The main advantages it delivers for renewable energy include:
Enhanced Efficiency:
Photo chemical etching allows for producing intricate and lightweight titanium components with precise geometries. Using lightweight components in renewable energy technologies like wind turbines and solar panels improves performance and energy output by reducing weight and drag.
Corrosion Resistance:
Titanium is highly corrosion-resistant, making it ideal for renewable energy applications exposed to harsh environmental conditions, such as offshore wind turbines and solar arrays. Photochemical etching preserves titanium’s inherent corrosion resistance, ensuring the longevity and durability of components in renewable energy systems.
Customization and Optimization:
Photochemical etching allows for the manufacturing of components tailored to specific renewable energy applications. Engineers can optimize the shape, size, and features of components to maximize efficiency and performance, resulting in more efficient and reliable renewable energy systems.
Cost-Effectiveness:
Compared to traditional machining methods, photochemical etching of titanium parts offers cost-effective solutions for renewable energy applications. The digital nature of the process allows for rapid prototyping and iterative design improvements without the need for expensive tooling, reducing development costs and time to market.
Scalability:
As a highly scalable process, photochemical etching is proven for both small-scale and large-scale production of titanium components for renewable energy systems. Whether producing individual prototypes or mass-producing components for commercial installations, the process offers consistent quality and precision at scale, ensuring reliable performance in critical applications.
Reduced Environmental Impact:
Compared to traditional machining methods, photochemical etching minimizes waste and energy consumption, aligning with the sustainability goals of the renewable energy sector. Titanium is also a recyclable material, which further reduces the environmental footprint of photochemically etched components.
Design Versatility:
Photochemical etching enables the creation of complex and intricate designs that may be challenging or impossible to achieve with traditional machining methods. This versatility allows for innovative designs that improve the efficiency, reliability, and aesthetics of renewable energy systems.
Challenges in Manufacturing Titanium Components
Due to titanium’s unique properties, the manufacturing process is complex and challenging, especially when using traditional machining methods.
Titanium is renowned for its high strength, corrosion resistance, and low thermal conductivity, but these properties also make it notoriously difficult to work with using conventional techniques.
Due to its high hardness, machining titanium requires specialized equipment and tooling, which results in increased tool wear and machining forces. Titanium’s poor thermal conductivity also leads to thermal expansion and deformation during machining. At elevated temperatures, titanium is also highly reactive with oxygen and nitrogen, requiring stringent environmental controls to prevent contamination and ensure the quality of the component.
With these complexities contributing to longer lead times, higher production costs, and reduced efficiency in traditional manufacturing processes, there is a growing demand for advanced manufacturing technologies, such as photochemical etching. With its unique ability to overcome these challenges, photochemical etching is the only process that can consistently achieve precise, cost-effective fabrication of titanium parts.
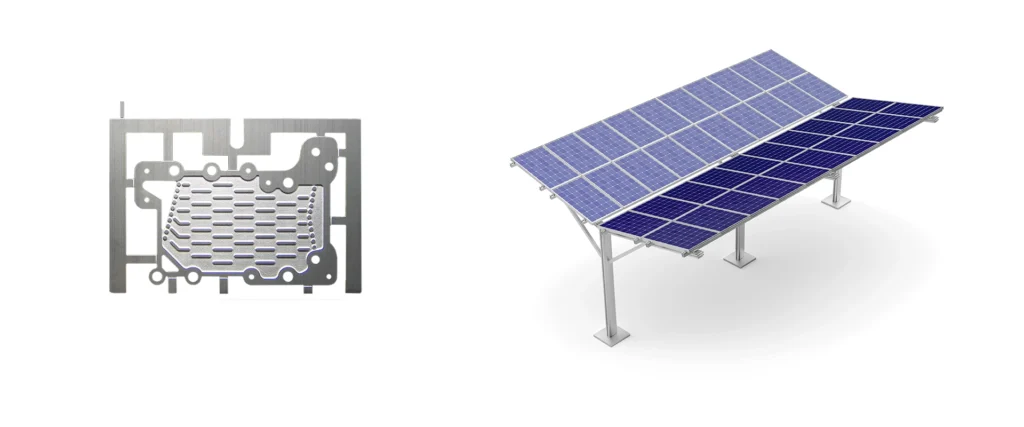
Shaping the Future of Renewable Energy
As the demand for sustainable energy intensifies, materials and processes are constantly evolving, and a number of innovations are shaping the sector’s future.
Innovations in materials include the development of high-performance alloys optimized for enhanced durability and conductivity, which are crucial for applications in solar panels, wind turbines, and fuel cells.
Enhancements to the photochemical etching process, such as improved masking techniques and tighter tolerances, enable the creation of intricate designs with unparalleled precision, facilitating the production of more efficient and reliable renewable energy components.
As manufacturing technology meets material science, photochemical etching will continue to play a crucial role in driving the transition to cleaner, greener energy.
Pioneers in Titanium Etching
With the renewable energy sector rapidly growing as the world looks to shift towards a greener future, the need for delicate, titanium-etched components crucial for the technologies driving this shift also increases.
With the challenges titanium etching presents, you need to work with a manufacturer with a proven track record of delivering lightweight, robust, and corrosion-resistant titanium parts.
As a leader in the renewable energy sector, the team at PEI works with a range of titanium grades, manufacturing high-quality, reliable components used in critical applications across the sector. Our advanced titanium etching process allows us to provide pure titanium anode and cathode plates for fuel cells, oxygen generators, hydrogen generators, and pure titanium bipolar electrolyser plates for the solar and energy generation markets.
If you need delicate titanium components proven to perform in renewable energy applications, we can help. Contact us today to discuss your project or request a quote.