In this article, we look at the tools, technology and processes required for precision and the crucial role precision metal parts play in reducing errors in precision mechanical assemblies.
In modern metal manufacturing, precision is not just a luxury — it’s a necessity. Precision serves as the foundation of quality and innovation. Beyond just accuracy, precision encapsulates the tight tolerances, intricate designs, and flawless surfaces required when producing components for today’s leading industries. Every minute detail must be carefully analyzed and flawlessly executed to deliver products that align perfectly, function optimally, and endure the test of time.
PEI stands at the forefront of precision metal fabrication, ensuring that assembly lines across industries benefit from accuracy. But how exactly do precision metal parts reduce assembly errors?
Precision metal parts fit seamlessly in assemblies due to their precise construction, reducing the risk of misalignments or inefficiencies. But that’s just the start.
In this article, we look at the tools, technology and processes required for precision and the crucial role precision metal parts play in reducing errors in metal assemblies.
The Basics of Precision Metal Parts
When it comes to metal manufacturing, precision metal parts represent the pinnacle of craftsmanship and meticulous engineering. These components are characterized by their intricate design, impeccable dimensional accuracy, and exceptionally tight tolerances.
The production of precision metal parts requires a deep understanding of materials, cutting-edge technologies, and a relentless commitment to quality.
Precision metal parts are crafted using advanced techniques such as CNC machining, EDM (Electrical Discharge Machining), waterjet and laser cutting, as well as Photo-Chemical Machining (PCM) to achieve unparalleled levels of accuracy and consistency.
Precision metal parts are crafted using advanced techniques such as CNC machining, EDM (Electrical Discharge Machining), waterjet and laser cutting, as well as Photo-Chemical Machining (PCM) to achieve unparalleled levels of accuracy and consistency.
These parts play critical roles across a range of leading industries, from aerospace and automotive to medical devices and electronics, where their flawless construction ensures seamless assembly, reliable functionality, and longevity.
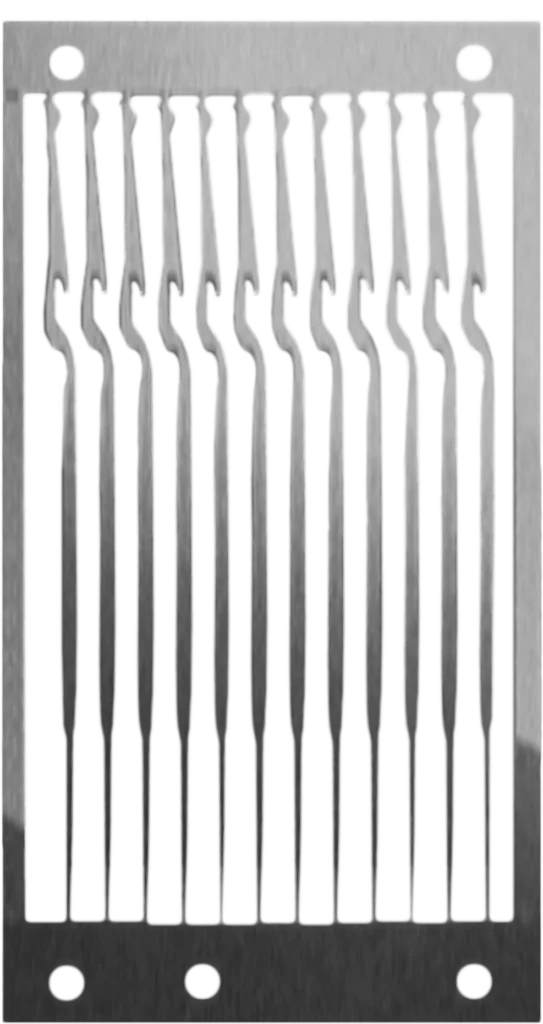
The characteristics of precision metal parts
Precision metal parts have a number of common characteristics that ensure optimal functionality and seamless assembly. They include:
Tight Tolerances:
Precision metal parts are crafted with incredibly narrow tolerances, ensuring minimal deviation from the intended specifications.
High Dimensional Accuracy:
These parts exhibit exceptional precision in terms of size, shape, and geometry, meeting exacting requirements down to micrometer levels.
Complex Geometries:
Precision metal parts often feature intricate and complex designs, challenging the limits of manufacturing capabilities.
Superior Surface Finish:
A hallmark of precision, these parts boast flawless surface finishes, free from imperfections that could impact performance or aesthetics.
Minimal Assembly Variability:
Precision metal parts fit seamlessly in assemblies due to their precise construction, reducing the risk of misalignments or inefficiencies.
Consistency in Reproduction
Each instance of a precision metal part mirrors the others with high consistency, ensuring uniformity across large-scale production.
Material Expertise:
The choice of materials for precision metal parts is crucial, considering factors such as strength, durability, and compatibility with intricate manufacturing processes.
Advanced Manufacturing Techniques:
Precision is achieved through cutting-edge methods like CNC machining, EDM, laser cutting, chemical machining (or etching) and additive manufacturing, which enable meticulous control over every detail.
Rigorous Quality Control:
Manufacturing precision metal parts demands rigorous quality assessment to identify and rectify even the slightest deviations at every stage.
Critical Industry Applications:
These parts find use in industries where reliability is paramount, such as aerospace, medical devices, electronics, and automotive engineering, supporting safety and innovation.
The most common materials used for precision metal parts include:
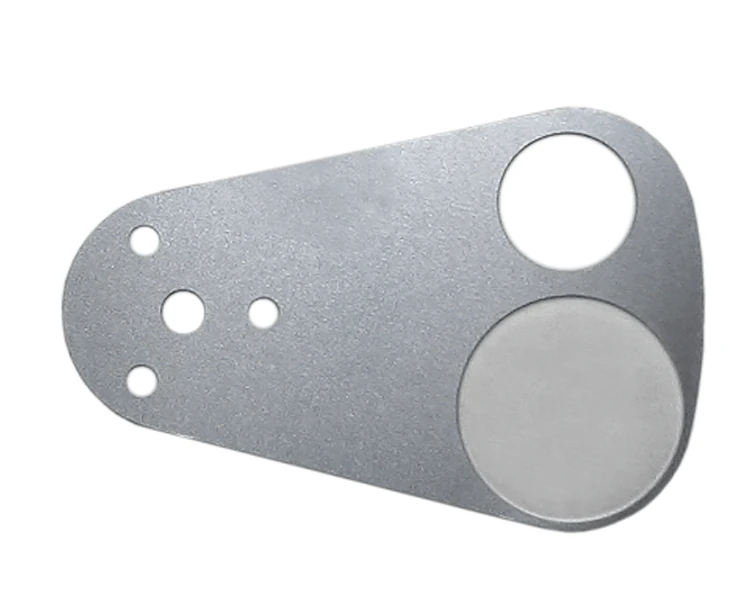
Stainless steel
Due to its corrosion resistance and mechanical strength
ex: 316 Stainless Steel Aerospace Thrust Spring
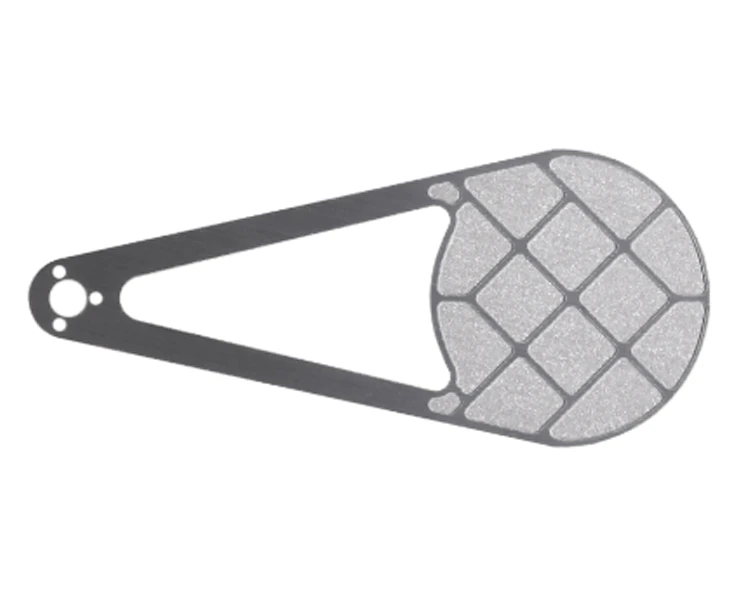
Aluminum
Due its lightweight properties and versatility
ex: Aluminum Precision Etched Part
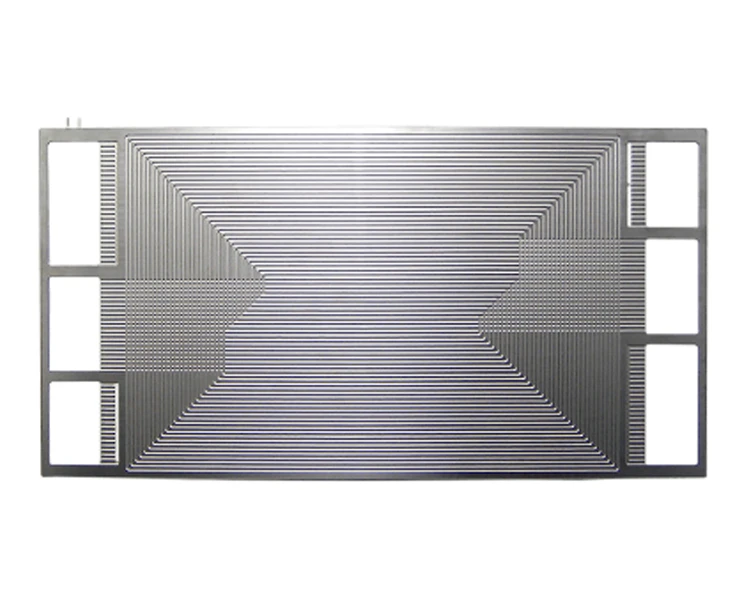
Due to its remarkable strength-to-weight ratio and biocompatibility
ex: Titanium Bipolar Electrolyzer Plate (Bottom Surface)
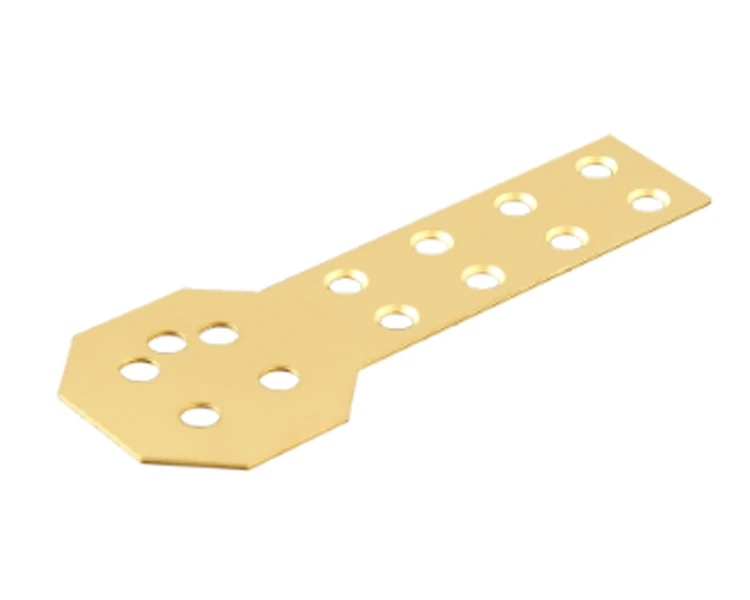
Alloys
Due to their superb heat and corrosion resistance in extreme environments
ex: Alloy 42 Gold Plated Precision Part
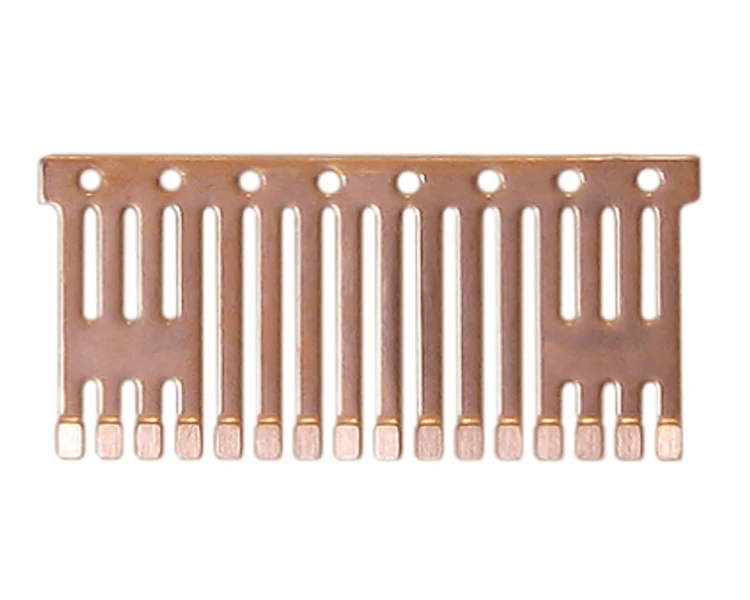
Copper
Due to its exceptional conductivity
ex: Copper Etched Lead for High Power Electronics
The selection of these materials is a meticulous process tailored to the specific demands of each part’s intended function, ensuring that the resulting precision metal components provide durability, performance, and reliability.
The power of precision metal fabrication:
How precision metal parts reduce assembly errors
Precision metal parts are integral to flawless manufacturing processes because they mitigate assembly errors. Engineered to exacting specifications, these parts exhibit consistently accurate dimensions and tight tolerances. As a result, during assembly, the parts align seamlessly, leaving little room for misfit or misalignment. Precision enables components to interlock precisely, reducing the need for adjustments and minimizing errors.
Precision metal parts:
Ensure consistent fit and finish — PEI’s photochemical machining process ensures every metal part adheres to exact specifications, ensuring a consistent fit and finish, eliminating the chances of assembly errors.
Reduce the need for adjustments and recalibrations — Precision parts substantially diminish the necessity for adjustments and recalibrations, streamlining assembly processes and enhancing overall operational efficiency.
Minimize material wastage — Precision parts lead to fewer defective products and reduced material wastage, ensuring both economic and environmental benefits.
The Role of Precision in Assembly Success
The role of precision in assembly success is irreplaceable, as it guarantees that components fit seamlessly and function optimally, minimizing errors and fostering the creation of flawless end products.
Precision parts not only ensure a perfect fit but also lead to quicker assembly processes, reducing production times and costs. Furthermore, precision metal components ensure accurate fitments and reliable functionality, mitigating risks and maintaining critical application integrity.
The perfect fit and optimal performance of precision parts minimize friction and mechanical stress, thereby reducing wear and tear on the components. This extends the longevity of products and significantly decreases the frequency and intensity of maintenance requirements, resulting in enhanced durability and cost-effective operation over the product’s lifespan.
Why Opt for Photochemical Machining For Metal Parts
When it comes to precision metal fabrication, one process has rapidly gained in popularity due to the vast number of advantages it offers. Photochemical Machining (PCM), also known as photochemical etching or photo etching, has emerged as a proven process for precision, combining speed, repeatability, and efficiency to deliver exceptional results.
Photochemical etching is the perfect process when you want or need:
- Reduced Set-Up Costs (only cost is a phototool)
- Rapid Turnaround (ideal for prototyping new projects)
- To Avoid the Expense and Time Delay for Secondary Operations (no need for deburring or annealing)
- To Create Parts from Difficult-to-Machine Materials like Titanium
- Precision, Precision, Precision
- Repeatability, Repeatability, Repeatability
PEI’s Precision Products Division offers industrial designers and electrical/mechanical design engineers, working for a myriad of different OEMs, the opportunity to create precision parts at competitive prices. Our history of engineering excellence ensures that your concept and design will be understood as our design staff offers unparalleled photo-etching expertise that adds value while lowering total project costs.
The key advantages of photochemical etching at PEI include:
- Rapid Prototyping
- Low cost tooling
- No Burrs
- No Stresses
- No Effect on Magnetic Properties
- No Deformation
- No Tool Wear
- Precise Control of the “Z” (depth) Dimension
Beyond Precision Metal Part Manufacturing: PEI's Finishing Services
Renowned for their leadership and innovation in precision metal part manufacturing, the team at PEI also specialize in a wide range of finishing services that include:
- Assembly
- Forming
- Heat treating
- Plating
- Polishing
- Silkscreening
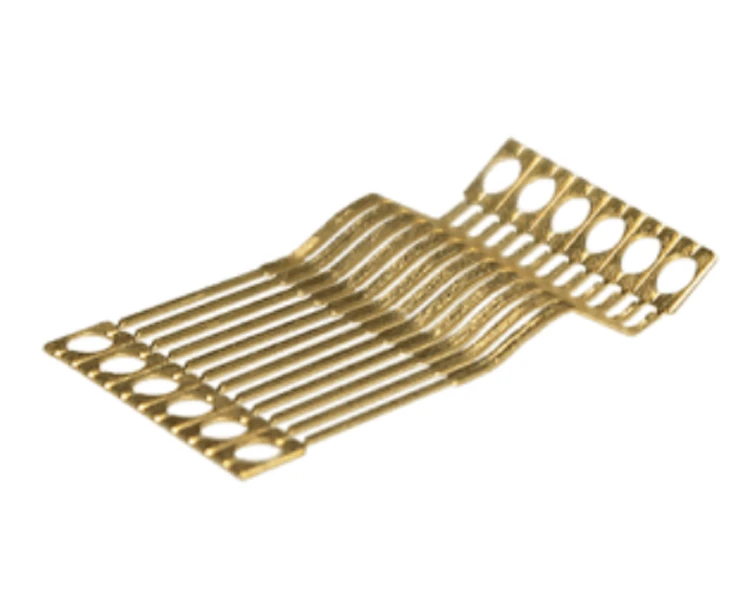
Your Proven Partner for Precision
Industry leaders in photochemical etching, PEI has fast built a reputation for delivering highly precise metal parts to a myriad of industries. With a commitment to excellence that extends to everyone they work with, they’ve become the trusted partner for precision parts for the aerospace, automotive, medical and electronics industries, to name a few.
If you need a proven partner for metal part manufacturing or assembly needs, you can’t go past the team at PEI. Request a quote and discover the PEI difference for yourself.