The world is in the midst of an energy revolution with a global shift towards cleaner, more sustainable power sources.
As the demand for sustainable energy solutions continues to surge, so does the need for high-efficiency, custom-made components such as fuel cells, metallic bipolar plates, wind turbine parts, solar panels, fuel cell stacks, and energy storage systems.
With its cutting-edge technologies and materials, precision metal manufacturing is playing a pivotal role in producing the intricate and durable components required for renewable energy systems. And one manufacturing process stands out above the rest – photochemical etching.
Here at Photofabrication Engineering (PEI), we lead the way in precision metal manufacturing for the renewable energy industry, producing photochemically-etched Bipolar Electrolyser plates in a wide variety of metals, including stainless steel, pure titanium, and other non-corrosive metals, for the solar and energy generation markets. And that’s just the start.
In this article, we look at the advantages of photochemical machining, the parts it can produce, and the reasons why it’s revolutionizing the renewable energy industry.
What is Precision Chemical Machining (PCE)?
Precision Chemical Machining (PCE), also known as photochemical machining, chemical blanking, or chemical milling, is a highly precise, cost-effective metal machining process used to produce complex components from a wide range of metals.
In PCE, materials are selectively removed from a metal sheet or plate using chemical reactions and photoresist masks. A light-sensitive photoresist is applied to the metal surface first. A detailed pattern of the desired part is then transferred onto the photoresist through photolithography. When exposed to light, photoresist hardens, protecting some areas while leaving others exposed. Chemical etchants are then applied to dissolve the unprotected metal, leaving behind the precise and intricate shape of the component.
With its ability to produce complex, burr-free, and highly consistent parts, Precision Chemical Machining has quickly become the preferred method in industries requiring intricate metalwork, such as aerospace, electronics, and medical device manufacturing. And the renewable energy industry is no different. The low-cost process allows for the mass production of complex parts for a wide range of uses.
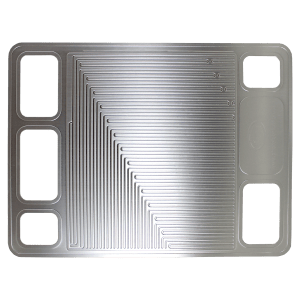
The production of precision metal parts requires a deep understanding of materials, cutting-edge technologies, and a relentless commitment to quality.
Precision metal parts are crafted using advanced techniques such as CNC machining, EDM (Electrical Discharge Machining), waterjet and laser cutting, as well as Photo-Chemical Machining (PCM) to achieve unparalleled levels of accuracy and consistency.
Precision metal parts are crafted using advanced techniques such as CNC machining, EDM (Electrical Discharge Machining), waterjet and laser cutting, as well as Photo-Chemical Machining (PCM) to achieve unparalleled levels of accuracy and consistency.
These parts play critical roles across a range of leading industries, from aerospace and automotive to medical devices and electronics, where their flawless construction ensures seamless assembly, reliable functionality, and longevity.
PCE in Renewable Energy: An Overview
Photochemical etching (PCE) has been increasingly integrated into the renewable energy sector, where it plays an important role in developing efficient renewable energy systems. Here’s how PCE is making an impact:
Solar Panels:
PCE is used to manufacture precision components such as busbars, connectors, and heat sinks for solar panels. These components must meet exacting tolerances to optimize energy conversion and heat dissipation. PCE’s ability to produce intricate patterns and shapes with high precision ensures the reliability and performance of solar panels.
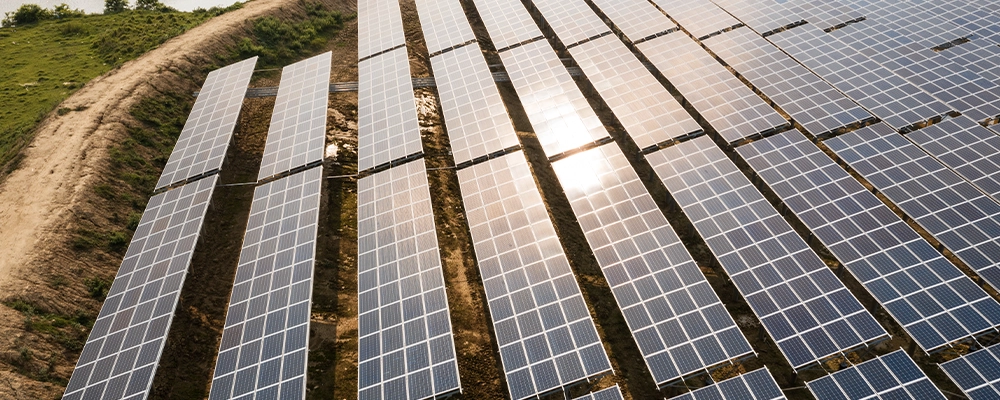
Bipolar Plate Electrolyzers:
Bipolar plate electrolyzers are an integral part of electrolysis systems used in the production of hydrogen via water electrolysis. Precision metal manufacturing techniques, such as PCE, are employed to create these plates from materials like stainless steel or titanium. These plates facilitate the efficient flow of electrical current through the electrolysis cell while separating the hydrogen and oxygen gasses produced. Precision photochemical etching ensures that the channels and gas diffusion structures on the plates are precisely aligned, enabling optimal performance and longevity of the Bipolar plate electrolyzer.
At PEI, our photochemical etching process allows very large, very thin single- or double-sided plates to be etched without incurring the stresses typical of other machining methods. Dimensions can be held to extremely high tolerances, and the process yields exceptionally smooth surfaces and channels (even with multiple channel depths on the same plate), free of burrs and other surface irregularities.
Wind Turbine Parts:
Numerous precision components are required for wind turbines, such as gears, bearings, and electrical contacts. PCE ensures wind turbines’ smooth and efficient operation by producing these parts with exceptional accuracy. PCE also enables the creation of lightweight yet durable components, enhancing energy output and turbine longevity.
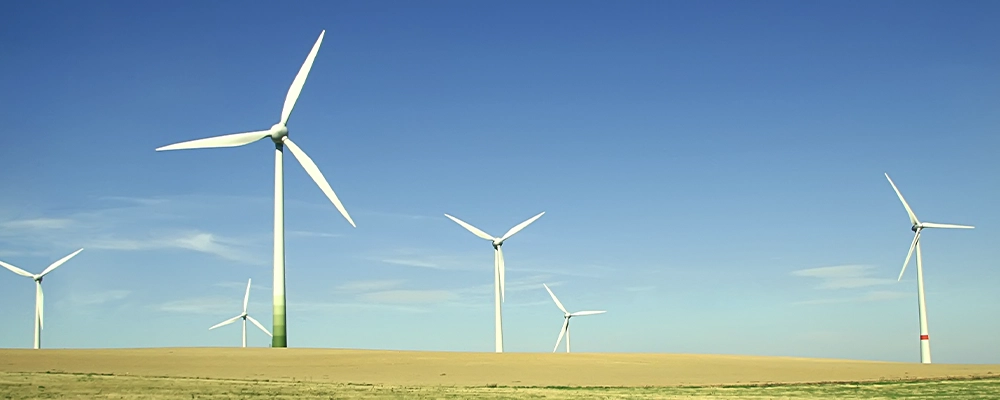
Energy Storage Systems:
In the renewable energy sector, energy storage systems stabilize the grid and ensure power availability during intermittent energy generation. PCE is utilized to manufacture components for energy storage devices like lithium-ion battery connectors and heat sinks, contributing to the efficiency and safety of these systems.
Proton Exchange Membranes (PEMs):
PEMs, also known as polymer electrolyte membranes, are critical components in proton exchange membrane fuel cells (PEMFCs), which are widely used in renewable energy applications, particularly in transportation and stationary power generation. Precision manufacturing techniques like PCE are employed to produce thin and uniform membrane electrode assemblies (MEAs) from materials like perfluorosulfonic acid (PFSA) polymer membranes. Precision is essential to control the thickness and porosity of the membrane electrode assembly, directly affecting its proton conductivity and overall efficiency in converting hydrogen into electricity. Accurate cutting and shaping of MEAs ensures their compatibility with other fuel cell components.
Hydrogen Fuel Cells:
When it comes to fuel cell technology, hydrogen fuel cells and PEM fuel cells are leading the way. Both delivering promising clean energy technology, PCE is employed to create precise flow plates and fuel cell bipolar plates that enable efficient gas distribution and electrical conductivity within fuel cells, making them more reliable and cost-effective for renewable energy applications.
Photofabrication Engineering (PEI) etches pure titanium to create anodes and cathodes for the fuel cell industry. As the leading expert in etching exotic materials and titanium for a broad variety of solar and energy generation applications (including fuel cells, batteries, and nuclear and desalination systems), PEI’s unique capabilities allow us to etch metals to multiple depths without the resist failures common to this etching process.
Wave and Tidal Energy:
PCE is used to fabricate components for wave and tidal energy generators, which harness the power of ocean currents. This includes the production of specialized materials and components that can withstand harsh marine environments while maximizing energy conversion.
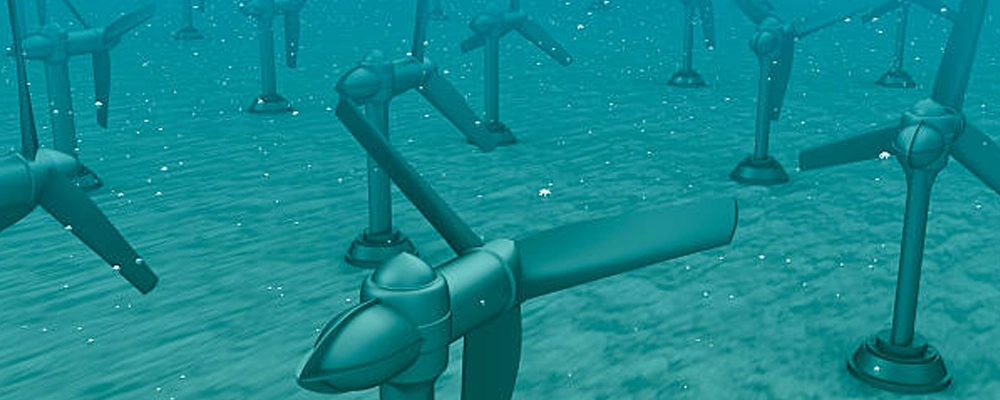
Hybrid and Electric Vehicles:
As the automotive industry shifts towards electric and hybrid vehicles, PCE is used to manufacture intricate components like electrical connectors and battery terminals. These components contribute to the efficiency and safety of electric propulsion systems, aligning with the renewable energy objectives of reducing greenhouse gas emissions.
Bipolar Plates:
Metallic bipolar plates are fundamental components in various types of fuel cells, including PEMFCs and solid oxide fuel cells (SOFCs). They serve as current collectors and separators between individual cells in a fuel cell stack. PCE is used to create these plates from materials like stainless steel or graphite, ensuring uniform distribution of reactant gasses and electrical current, minimizing energy losses, and maximizing the overall efficiency of the fuel cell.
By integrating PCE into the renewable energy sector, manufacturers can produce high-quality, precision components that are essential for the reliability and performance of renewable energy systems. This technology ensures that the renewable energy sector can continue to grow and contribute to a sustainable and cleaner energy future.
The Advantages of PCE in Renewable Energy
Precision Chemical Machining (PCE) is revolutionizing the way we harness and utilize sustainable energy sources.
A game-changer in the renewable energy sector, PCE offers a host of advantages that meet the demands of renewable energy applications. They include:
Unparalleled Precision: Renowned for its ability to produce highly precise and intricate metal components, the process can achieve tolerances as tight as ±0.001 inches (±0.0254 mm) or even better. This level of precision ensures that the final parts meet exacting specifications, making PCE ideal for the renewable energy industry where precision is critical.
Reduced Environmental Impact: The PCE manufacturing process utilizes non-toxic chemicals to etch the metal, and reducing material waste minimizes the environmental impact. PCE can also recycle and reuse certain chemicals, further reducing its environmental impact.
Intricate Geometries: With PCE, you can produce complex and intricate component designs that may be challenging or cost-prohibitive with other manufacturing methods. It is incredibly versatile and can easily create features like fine holes, slots, and patterns perfect for a wide range of applications. PCE can also afford multiple depths on the same plate design.
Cost-Effective for Prototyping: PCE is cost-effective for producing prototypes and small production runs. Tooling costs are relatively low compared to other precision manufacturing methods like stamping or die-cutting, making it an attractive choice for product development and testing.
Cost-Effective for Prototyping: PCE is cost-effective for producing prototypes and small production runs. Tooling costs are relatively low compared to other precision manufacturing methods like stamping or die-cutting, making it an attractive choice for product development and testing.
Quick Turnaround: Due to its digital and photolithographic processes, PCE offers short lead times. Design changes can be implemented Due to its digital and photolithographic processes, PCE offers short lead times. Design changes can be implemented in weeks instead of months, allowing for rapid iterations and reducing time-to-market for new products., allowing for rapid iterations and reducing time-to-market for new products.
Wide Material Compatibility: PCE can be applied to a wide range of metals and alloys, including stainless steel, copper, aluminum, and more. This versatility enables manufacturers to choose the most suitable material for their specific application without compromising on precision.
Customization and Design Flexibility: PCE allows for easy customization and design flexibility. Design modifications can be made without the need for costly tooling changes, making it ideal for adapting to evolving project requirements.
Leaders in Precision Metal Manufacturing for the Renewable Energy Industry
Renowned for producing photochemically etched Bipolar Electrolyser plates in stainless steel, titanium, and other non-corrosive metals for solar and energy generation, Photofabrication Engineering (PEI) is a leader in precision metal manufacturing for the renewable energy industry. We also etch pure titanium to create anodes and cathodes for the fuel cell industry.
As the leading expert in etching exotic materials and titanium for a broad variety of solar and energy generation applications (including fuel cells, batteries, and nuclear and desalination systems), PEI’s unique capabilities allow us to etch metals to multiple depths without the resist failures common to this etching process.
Some examples of our work include:
Case Studies
Lorem ipsum dolor sit amet, consectetur adipiscing elit, sed do eiusmod tempor incididunt ut labore et dolore magna aliqua. Ut enim ad minim veniam, quis nostrud exercitation ullamco laboris nisi ut aliquip ex ea commodo consequat. Duis aute irure dolor in reprehenderit in voluptate velit esse cillum dolore eu fugiat nulla pariatur. Excepteur sint occaecat cupidatat non proident, sunt in culpa qui officia deserunt mollit anim id est laborum.
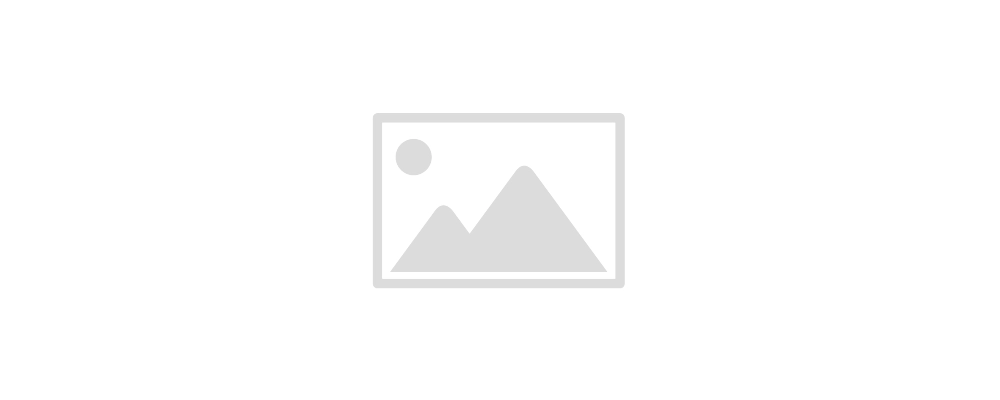
Shaping the Future of the Renewable Energy Industry
Potential advancements and innovations in Precision Chemical Machining (PCE) hold immense promise for the renewable energy industry. As PCE technology continues to evolve, we can anticipate even greater precision and efficiency in manufacturing critical components for renewable energy systems. This could lead to the development of lighter and more durable materials, improved energy conversion rates, and increased system reliability.
As PCE becomes more environmentally sustainable through the adoption of greener chemicals and recycling processes, it aligns seamlessly with the renewable energy sector’s commitment to sustainability and reduced environmental impact. These advancements have the potential to accelerate the growth of renewable energy, making it a more accessible and viable source of clean power for a sustainable future.
Titanium fuel cells, oxygen generators, and hydrogen generators represent a giant step in the development of clean energy technology. Used in industries such as aerospace, automotive, medical systems, biotechnology, wastewater treatment, and pulp and paper (bleaching), these products are becoming increasingly cost-effective as well as environmentally desirable. PEI’s unique ability to produce lightweight photoetched titanium parts in production quantities allows solar product manufacturers to meet high-volume, low-cost manufacturing goals to accelerate the commercial viability of fuel cells as well as oxygen and hydrogen generators, as mandated by the U.S. Energy Department.
If you’re looking for a precision partner in renewable energy, PEI can help. We provide manufacturers with a complete turnkey operation, including toolmaking, plating, and forming, so we can make deliveries with extremely quick turnaround times at competitive prices.
Get in touch with us today or request a quote.