As precision metal manufacturing continues to evolve rapidly, more industries are looking to push the boundaries of design. But with the demand for intricate and complex designs growing, one process stands above the rest due to its ability to offer unmatched design flexibility with precision and efficiency.
Photochemical etching is known for its design flexibility, making it a preferred choice for manufacturers looking to push the limits of creativity and innovation. Delivering both versatility and efficiency, photo etching enables the production of intricate and complex metal components with precision and accuracy.
Photofabrication Engineering, Inc. (PEI) has been a pioneering force in leveraging photochemical etching (PCE) to enhance design flexibility for a wide range of industries. Since 1968, we’ve continually pushed the boundaries of innovation, transforming intricate design concepts into precision-engineered metal parts with exceptional accuracy and efficiency.
In this article we explore the unique advantages photo etching delivers over traditional manufacturing processes and how this precision process is empowering designers and engineers to push the boundaries of creativity and innovation.
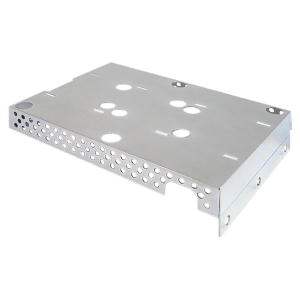
What is Precision Chemical Machining (PCE)?
Precision Chemical Machining (PCE), also known as photochemical machining or chemical milling, is a highly precise, cost-effective metal machining process used to produce complex components from a wide range of metals. Photochemical etching (PCE) stands out as a versatile and efficient manufacturing process due to the numerous advantages it offers over traditional methods such as laser cutting and water jet cutting.
The innovative photo etching process utilizes chemical etchants and precise masking to selectively remove metal from a substrate, enabling the production of intricate and complex metal components with precision.
Materials are selectively removed from a metal sheet or plate using a chemical reaction and photoresist mask as part of the process. A light-sensitive photoresist is applied to the metal surface first, allowing it to harden when exposed to UV light. This protects some areas while leaving others exposed.
Chemical etchants are then applied to dissolve the unprotected metal, leaving behind the component’s precise and intricate shape.
With its ability to produce complex, burr-free, and highly consistent parts from sheet metal, photo etching has quickly become the preferred method in industries requiring intricate metalwork with controlled material thickness, such as aerospace, electronics, and medical device manufacturing.
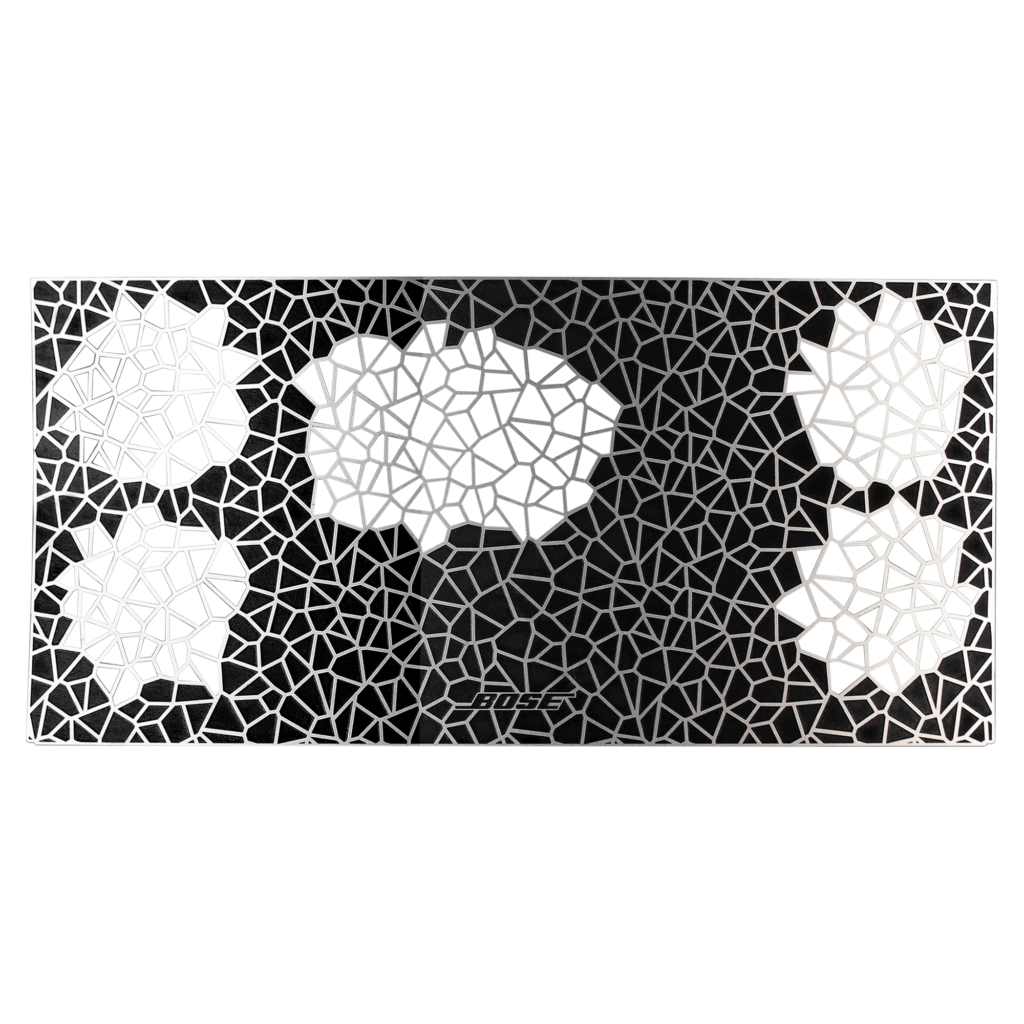
The Role of Design Flexibility
Design flexibility plays a crucial role in driving product innovation and development across industries. It allows manufacturers to respond quickly to changing market demands, customize products to meet specific customer requirements, and push the boundaries of design creativity.
In today’s fast-paced and competitive marketplace, the ability to adapt and iterate designs efficiently is essential for staying ahead of the curve and delivering cutting-edge solutions to consumers.
In the automotive sector, advancements in design flexibility have enabled the creation of sleeker, more aerodynamic vehicle designs that enhance fuel efficiency and performance. Within the medical field, design flexibility allows for the customization of medical devices and implants to match individual patient needs, leading to better outcomes and enhanced patient comfort.
Flexible design solutions are also revolutionizing the aerospace field. They enable the creation of lightweight yet robust aircraft components for use in critical aerospace applications.
Enhancing Design Flexibility with Photo Chemical Etching
For manufacturers seeking to push the limits of creativity and innovation, photochemical etching provides significant advantages in design flexibility.
Unlike traditional machining processes, which may be limited by tooling constraints and material properties, chemical etching allows for the easy creation of intricate geometries, fine features, and complex patterns. By leveraging advanced masking techniques and precise etching control, manufacturers can achieve remarkable levels of detail and precision in their components, opening up endless possibilities for design customization and optimization.
Photochemical etching also enables the production of components with varying thicknesses, intricate internal features, and burr-free edges, further expanding design possibilities and eliminating the need for secondary machining operations.
Design modifications can be made without the need for costly tooling changes, making it ideal for adapting to evolving project requirements. This level of design flexibility streamlines the manufacturing process and reduces costs and lead times, allowing manufacturers to bring products to market faster and more efficiently. The trusted team at PEI utilizes low-cost, easily produced film tooling that enables customers to explore design possibilities without the constraints of expensive tooling or lengthy lead times.
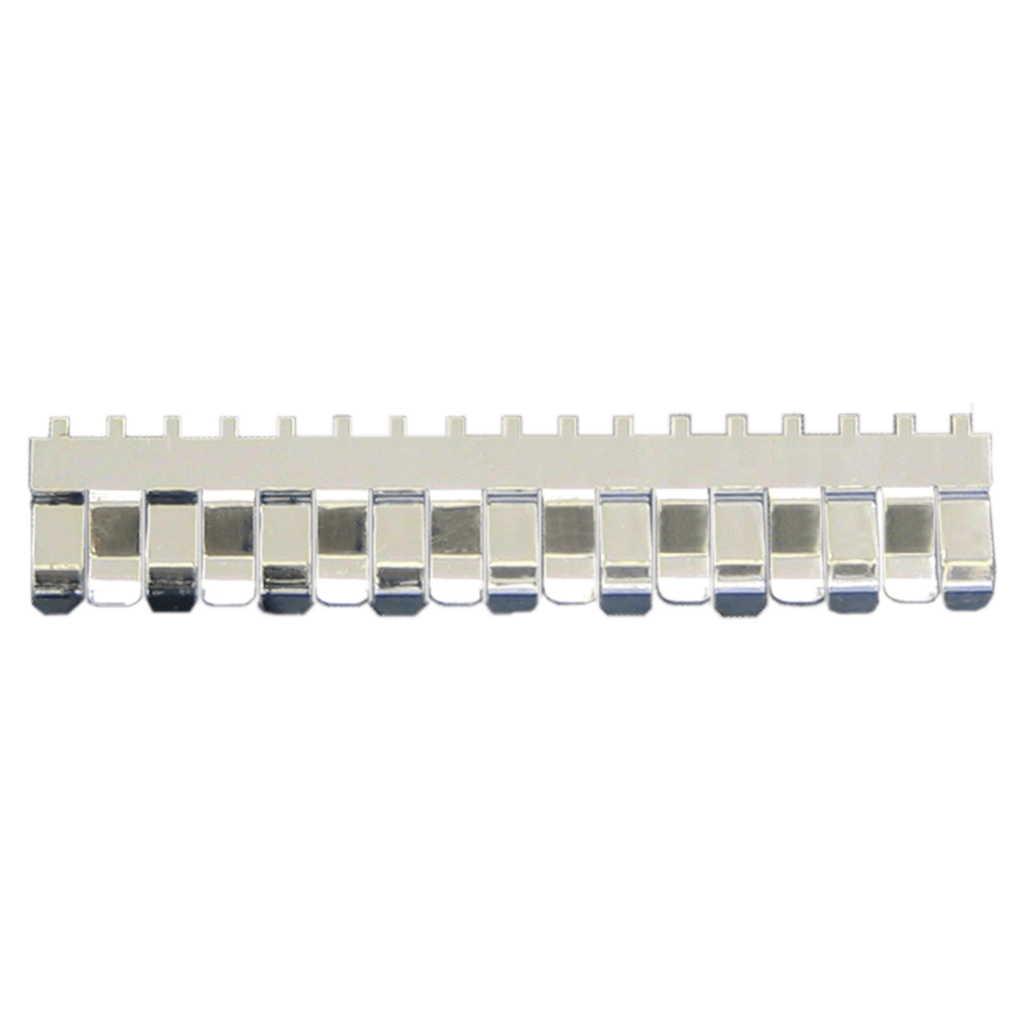
A Proven Precision Chemical Machining Process
PEI excels in providing extensive design flexibility through our proven etching process, enabling customers to bring their most intricate and complex designs to life with precision and efficiency. With our state-of-the-art facilities and decades of experience, we’ve refined the photo etching process to deliver optimal outcomes for our clients.
Our market-leading subtractive manufacturing process allows for the creation of intricate geometries, fine features, and complex patterns that are simply unattainable through traditional manufacturing methods.
Whether it’s prototyping new product concepts or mass-producing complex components, our team of skilled engineers and technicians works closely with clients to understand their unique design requirements and bring their vision to life.
Add to that PEI’s commitment to quality, precision, and customer satisfaction, and it’s easy to see why we’re a trusted partner for enhancing design flexibility through photochemical etching.
The Benefits of Using PEI for Precision Photo Etching
For over half a century, PEI has continually pushed the boundaries of innovation, transforming intricate design concepts into precision-engineered metal parts.
When you work with us, you can produce complex and intricate component designs that may be challenging or cost-prohibitive with other manufacturing methods. And the benefits don’t stop there. Other advantages of choosing PEI for precision photo chemical etching include:
Unparalleled Precision: We are renowned for our ability to produce highly precise and intricate metal components. Our proven process can achieve tolerances as tight as ±0.001 inches (±0.0254 mm) or even better. We are committed to quality and customer satisfaction and ensure that the final parts are delivered to meet your exacting specifications.
Cost-Effective Prototyping: Thanks to our low tooling costs, we’re the perfect partner for cost-effective prototypes and small production runs, making us an attractive choice for product development and testing.
Quick Turnaround: We offer short lead times due to our digital and photolithographic processes. Design changes can be implemented swiftly, allowing for rapid iterations and reducing time to market for new products.
Wide Material Compatibility: We’re experts in working with a wide range of metals and alloys, including stainless steel, copper, aluminum, and more. We’ll choose the most suitable material for your specific application without compromising on precision.
Shaping the Future of Design
As the demand for customized and high-quality components continues to grow, photochemical etching remains at the forefront of manufacturing technology, driving product innovation and pushing the boundaries of design creativity across industries.
A game-changer in enhancing design flexibility for various industries, photochemical etching will continue to empower manufacturers to innovate and differentiate their products not just in today’s competitive marketplace but the marketplaces of the future.
If you’re looking to bring your most intricate and complex designs to life with precision and efficiency, PEI can help. With the design flexibility through our photochemical etching process, our team of experienced engineers and technicians works closely with clients to understand their unique design requirements and bring their vision to life.
From prototyping to high-volume production, our PCE services are versatile and reliable for a wide range of industry applications.
Ready to turn your ideas into precision-engineered reality? Discover how we can support your next project by requesting a quote.