For industries that rely on the strength, durability, and performance of their components, titanium is a clear material choice. And it’s easy to see why.
Titanium is often called a wonder metal due to its lightweight, unmatched strength, and corrosion-resistant properties. But what truly sets this exceptional metal apart is the transformative process known as titanium etching. By photochemical etching titanium, the metal’s already remarkable properties are refined, increasing corrosion resistance and enabling intricate designs that defy conventional machining. These attributes make titanium and titanium alloys highly desirable materials for the production of high-precision, high-performance components.
Perfect for various applications within the aerospace, medical, defense, and electronics industries, titanium-etched components ensure performance and reliability in even the harshest environments.
As the trusted industry leader in titanium etching, the Photofabrication Engineering, Inc. (PEI) team has a long history of engineering excellence and a focus on providing titanium parts with the highest level of quality.
In this article, we look at the multitude of benefits titanium etching delivers and the diverse applications it offers leading industries worldwide.
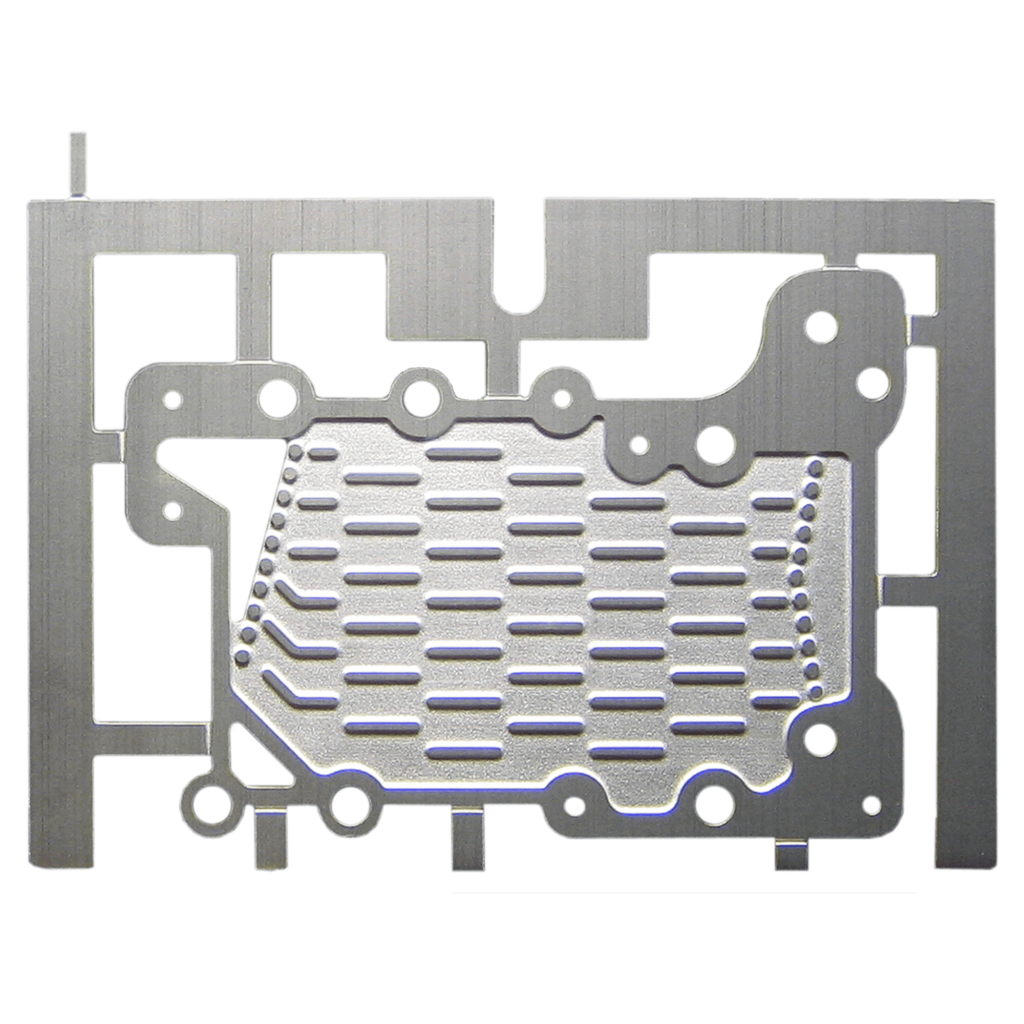
Unlocking the power of precision: the benefits of titanium etching
Titanium’s exceptional flexibility has made it a game-changer in precision metal manufacturing, enabling the creation of intricate, durable components across a range of industries.
This innovative photochemical etching process offers a range of benefits to both manufacturers and end users, making it the ideal choice for applications where precision, performance, and durability are non-negotiable.
- Precision and Control: With titanium etching, manufacturers can remove material with unparalleled precision and control. This level of accuracy is especially vital in applications where tight tolerances are required, such as fuel cells, oxygen generators, and hydrogen generators for renewable energy, custom medical implants, and microelectronics.
- Improved Surface Finish: Etching enhances the aesthetic and functional appeal of titanium components. Smoother surfaces not only enhance the visual allure but also reduce friction and wear in moving parts, leading to increased longevity.
- Customization: The adaptability of titanium etching makes it an ideal choice for industries requiring unique, non-standard components (aerospace, defense, and medical). Customizing the process to meet specific design requirements ensures that each piece meets its intended purpose.
- Enhanced Bonding: Etching doesn’t just stop at surface modification; it creates a textured surface that’s perfect for improving the adhesion of coatings, adhesives, or other materials. In sectors like medical devices and aerospace, where bonding strength is critical, this advantage is invaluable.
- Corrosion Resistance: Titanium is already renowned for its corrosion resistance, but etching takes it a step further. It enhances the material’s ability to withstand even the harshest environments, such as marine or chemical processing applications.
The titanium etching process
Photochemical etching is a precise and controlled technique used to produce highly accurate titanium parts. It begins with the selection of a suitable titanium chemical etching solution, often involving the use of hydrofluoric acid. This chemical etching transforms the metal surface of titanium components, selectively removing material to create intricate designs and textures that enhance the material’s remarkable corrosion resistance.
This titanium etching process offers excellent precision, repeatability, and scalability for etched titanium parts, making it an efficient and cost-effective method for producing high-quality titanium parts with complex geometries.
The key applications of titanium etching
Boasting a unique blend of strength, lightweight properties, corrosion resistance, and biocompatibility, etched titanium is the preferred choice for applications across various industries. These include:
Aerospace
In the aerospace industry, lightweight yet durable components are a must. Photochemical etching of titanium is relied on to deliver critical elements like aircraft frames, engine parts, and landing gear.
The precise control offered by etching ensures the safety and performance of these components, contributing to the efficiency and reliability of aerospace technology.
Renewable Energy
Titanium’s unique properties, such as its exceptional strength-to-weight ratio, corrosion resistance, and durability, make it an ideal material for producing intricate components crucial to renewable energy applications.
From solar panels and wind turbines to fuel cells and batteries, photochemically etched titanium components play a pivotal role in enhancing the efficiency and longevity of various renewable energy technologies.
PEI has become a leader in the renewable energy sector, providing pure titanium anode and cathode plates for fuel cells, oxygen generators, and hydrogen generators.
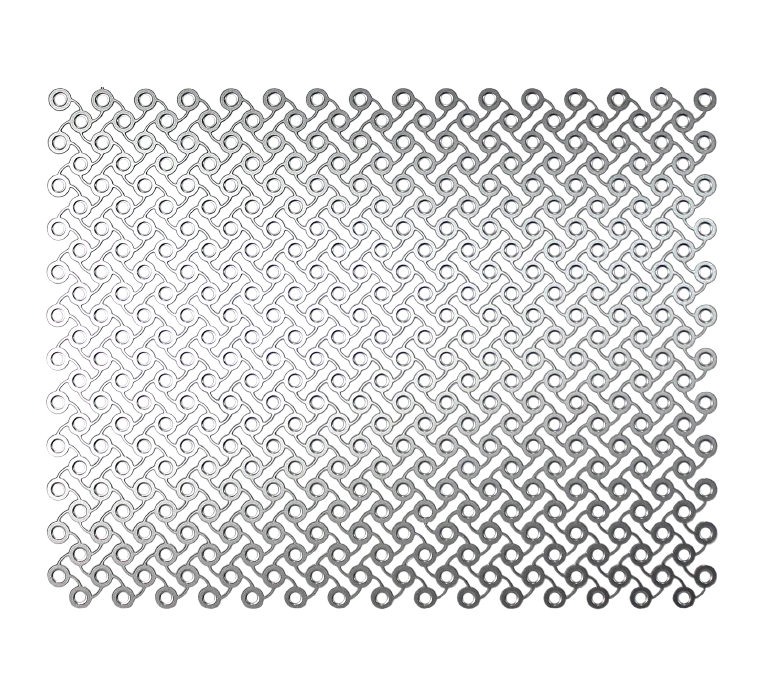
Medical
In the medical field, titanium etching enables the creation of vital implants such as maxiofacial surgical meshes, hip and knee replacements. The customized surface finish not only enhances aesthetics but also promotes osseointegration, allowing bones to securely merge with the implant. This unique bond enhances stability and longevity, turning titanium etching into a life-changing technology.
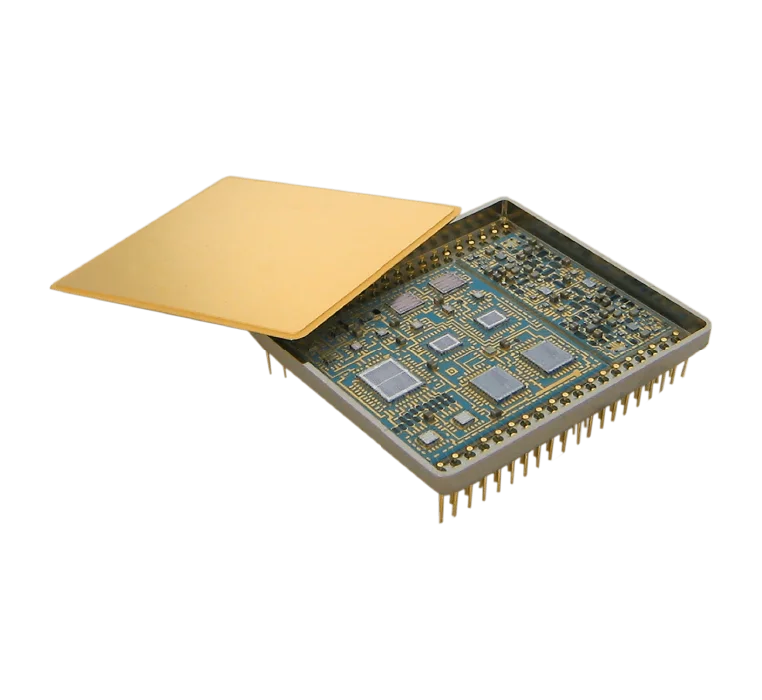
Electronics
In an industry where precision is paramount, the role of titanium etching in electronics cannot be overstated. Titanium etching is instrumental in the production of microelectromechanical systems (MEMS), sensors, and printed circuit boards. The process’s precision is revolutionizing the industry by ensuring intricate patterns and structures at the micro and nanoscale.
Chemical Processing
Titanium-etched components are an excellent choice for chemical processing due to their robust corrosion resistance. The etching process is used to craft tanks, pipes, and valves that can withstand the most corrosive environments, ensuring the longevity and safety of critical components.
Automotive
With titanium etching, lightweight parts can be created for the automotive industry that contributes to improved fuel efficiency. It’s also working behind the scenes, enhancing the aesthetics of cars through the production of both interior and exterior decorative elements.
Trusted experts in titanium etching
Here at PEI, we boast over 30+ years of experience creating intricate and precise titanium parts for various leading industries. Pioneers in laser cutting and etching pure titanium, our innovation and insight have opened up new possibilities for applications with their precision metal components.
As the trusted industry leader in titanium etching, our commitment to quality is unwavering, ensuring that every titanium component is crafted safely with unparalleled precision and durability while adhering to the rigorous standards set within each industry.
Because we make our own photochemical etching tools and have over 2,000 material part numbers in stock, we can offer quick turnaround at extremely competitive prices. Our proven photochemical etching process assures that tolerances can be held in all dimensions to within 10% of the material thickness, and changes in tooling design can be made quickly and cheaply.
Unlock the full potential of titanium with PEI’s advanced photochemical etching process. Contact the team or request a quote.